Moldtech, a leading company in the manufacturing of elements for concrete prefabrication, has taken a significant step in its global projection.
The client, a multinational with an impressive business trajectory of over 70 years, is a reference in the construction world and has been distinguished by its culture of entrepreneurship and innovation in the constant pursuit of new horizons. Recognized for its position in the ranking of the top 25 European groups in the construction industry, it currently operates in 23 countries, across three geographical areas: Europe, Africa, and Latin America.
The project reflects Moldtech‘s expansion and highlights the trust that clients place in the company due to its quality and personalized approach. It involves a comprehensive mobile factory that will focus on producing prefabricated concrete elements for civil engineering projects, encompassing the following elements and equipment:
- An MT20 mold for semi-dry box culverts, designed for high productivity of prefabricated concrete culverts, as it allows the use of semi-dry vibro-pressed concrete.
- Two self-supporting pre-stressing benches, to produce various types of pre-stressed beams for bridges and viaducts, with a prestress capacity of up to 400 tons.
- Mold for I-beams, composed of two moulds sides in the shape of an I with a quick fixing system with different positions for adjusting the size of the beam to be produced.
- A mobile hot water or steam boiler to improve concrete curing during periods of low temperatures in the area. High-performance hot water boilers are efficient and reliable equipment for producing hot water or steam, which is used to provide heating to the precast equipment.
- A Giraffe vehicle, designed for concrete transport and pouring. This self-propelled equipment solves the logistics problem in precast plants and provides an alternative to using overhead cranes for concrete transport.
- Two 2m3 pouring skips for concrete transport and pouring. The pouring skip consists of a bucket that allows transporting concrete from the mixing plant to the molds to be filled. The pouring skip can be transported either by forklift or by an overhead or by gantry crane.
- A 90º turner, designed to rotate prefabricated 3D concrete pieces (culverts and semi-culverts) 90º, from the molding position to the final placement position on-site.
The successful completion of this major project in Nigeria not only marks a significant milestone for Moldtech and its client but also strengthens their strategic collaboration in the global construction industry. With the installation of a complete portable factory and the provision of state-of-the-art equipment, both companies demonstrate their commitment to quality, innovation, and customer satisfaction. This achievement reflects Moldtech‘s ability to offer personalized and proficient solutions in the concrete prefabrication sector, while underscoring the experience and leadership of its client in executing large-scale infrastructure projects. Undoubtedly, this collaboration promises to continue harvesting successes and contribute to the sustainable development of the construction industry worldwide.
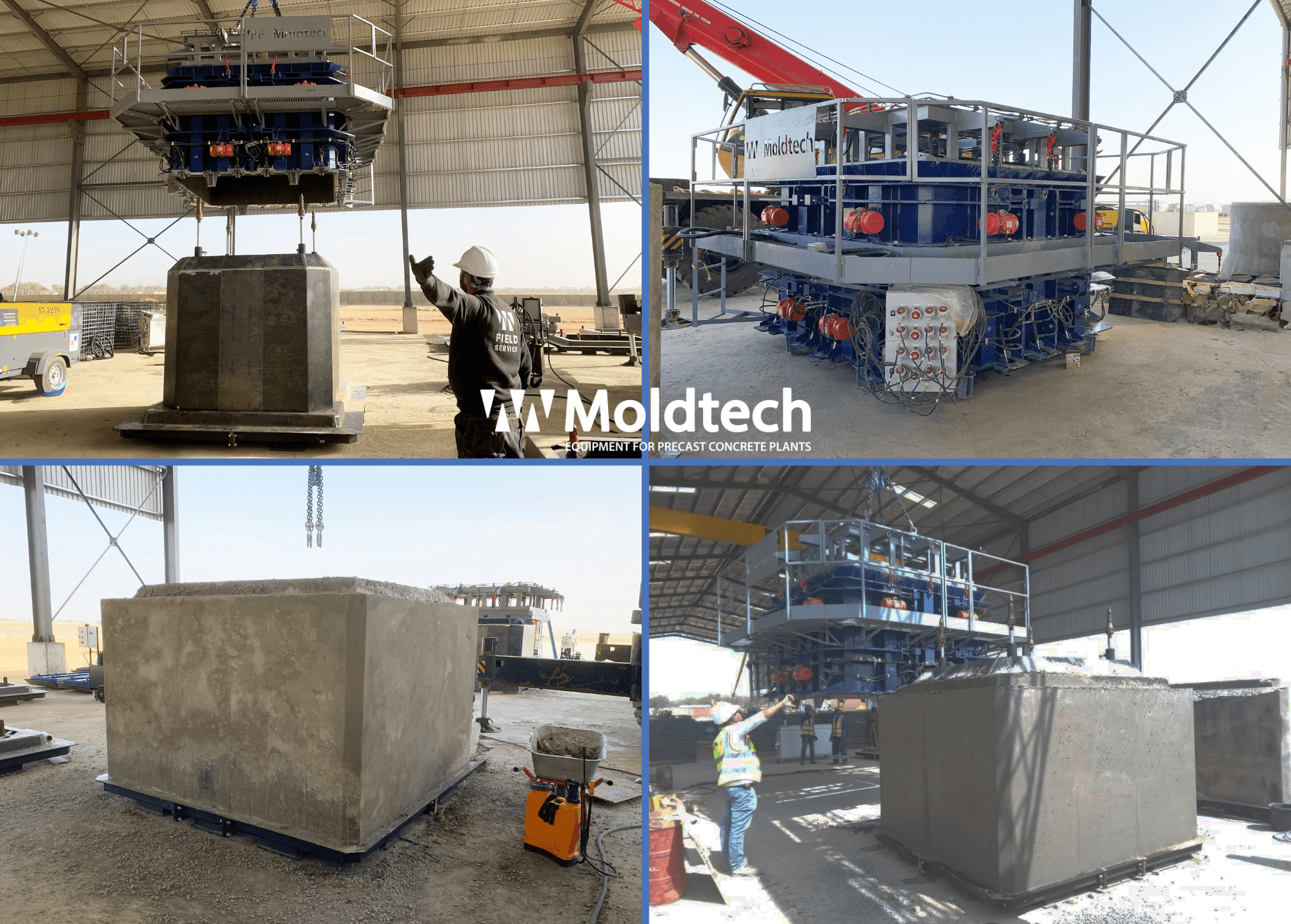
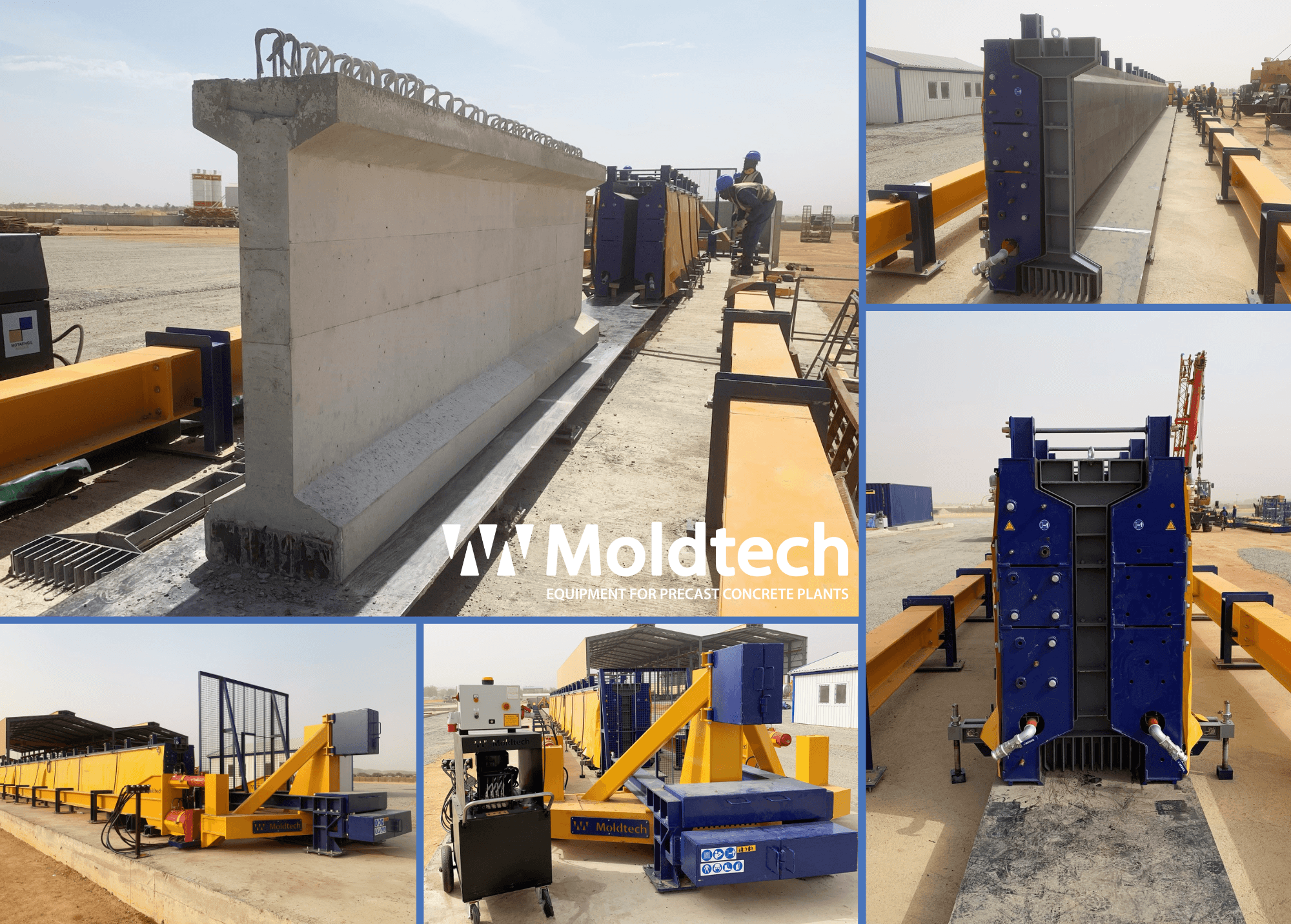
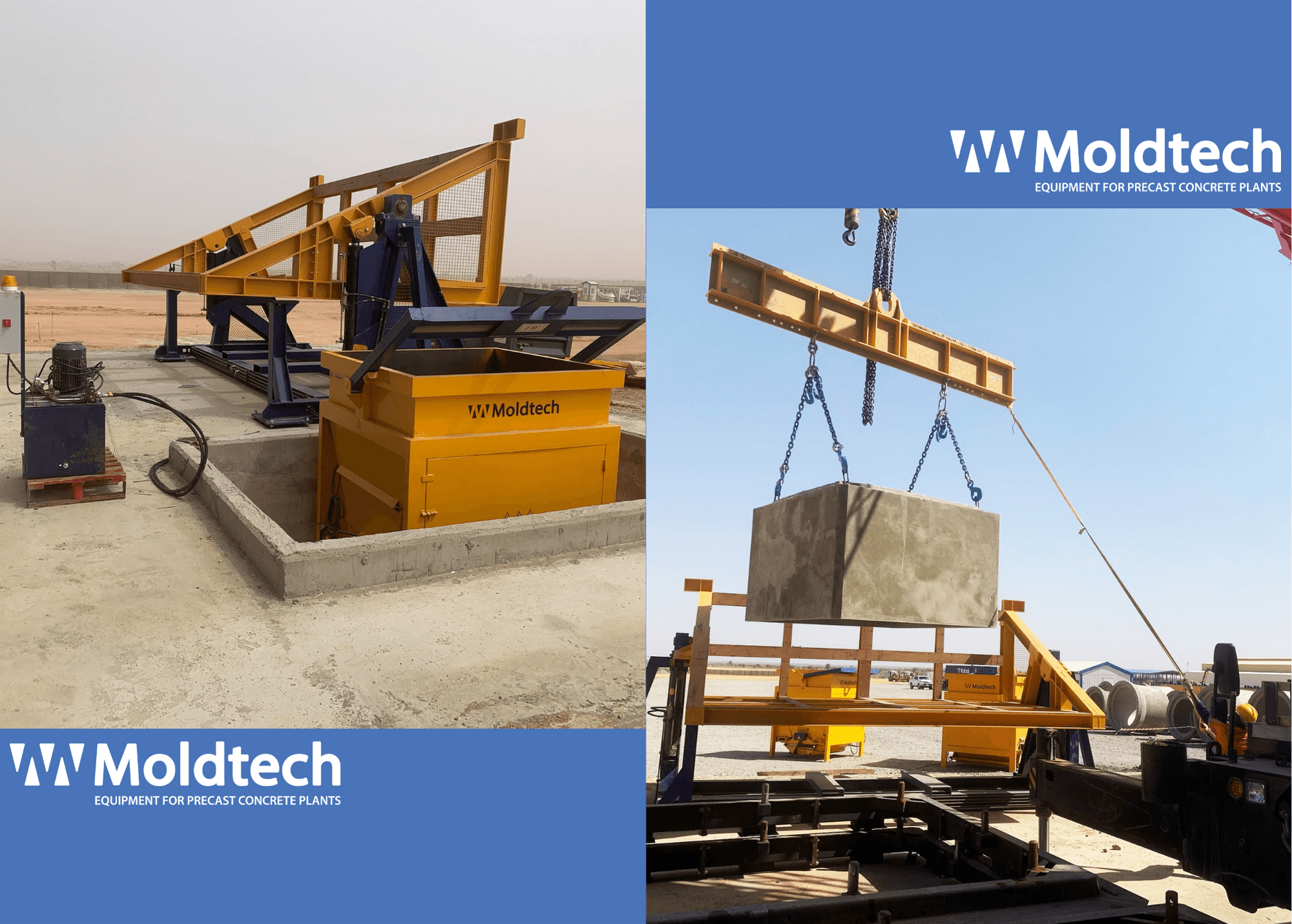
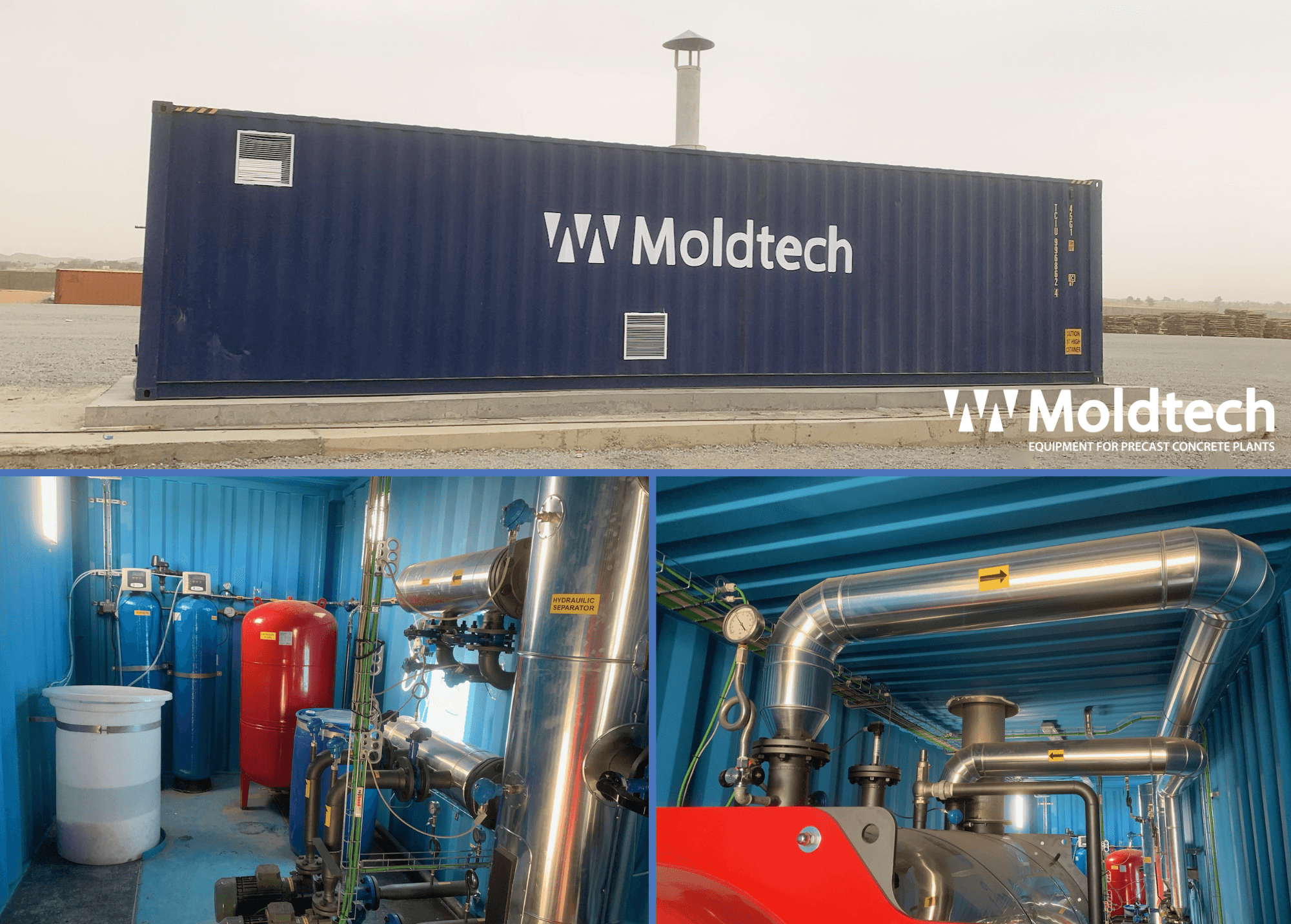