Moldtech’s major client, which is a leader in engineering and construction, is currently developing one of the country’s most ambitious infrastructure projects: the Alexandria Metro. In partnership with Colas Rail, this $1.39 billion project will completely transform the existing rail network into a modern metro system, covering 21.7 km and featuring 20 stations strategically located between the centre of Alexandria and the city of Abu Qir in the northeast part of the country. This effort, part of a plan to modernization of the transport in Egypt, represents a major step towards an efficient, fast and sustainable urban transport system, financed by international institutions such as the European Investment Bank (EIB), the European Bank for Reconstruction and Development (EBRD) and the Agence Française de Développement (AFD).
Main features of the Alexandria Metro Project
The Alexandria Metro will include elevated stations, some others on ground and few underground stations, allowing it to adapt to the needs of the city and minimise the impact on Alexandria’s dense urban traffic. In the first phase, the metro will span 21.7km from Misr station in the heart of the city to Abu Qir, providing fast and direct access between these key areas. The 20 stations in this phase will be designed to optimise the passengers flow, with several elevated stations complementing some station on ground floor and underground stations as well, allowing great connectivity in the public transport network.
For future phases, a 13.2 km underground tunnel is planned, which will increase operational speed and reduce travel timing. This underground section will be key for providing greater efficiency and sustainability, as it will reduce traffic congestion and promote the use of public transport in the area. Meanwhile, this project will also promote an environmentally friendly alternative.
Moldtech: equipment development for the metro in Alexandria Region
To achieve this state-of-the-art infrastructure, the project is supported by Moldtech, a leading manufacturer of precast concrete equipment, whose experience in civil engineering and industrial development projects around the world has been the key in the implementation of several important infrastructures. Moldtech has already supplied a complete factory of equipment specifically designed to produce “Box Girders”, which will be integrated into this new metro network, contributing to the precision of the construction. The production capacity of this system is essential for the success of the project, as it allows the production of large volumes of these precast elements with high quality standards.
Self-Supporting Prestressing System and Trough Beam Production Line
The scope of supply designed and manufactured by Moldtech includes two complete self-reacting lines which optimise the production of the above-mentioned prestressed Box Girders. These 2 production lines consist of active and passive heads at the ends of the corresponding self-reacting structure. This system allows the production of prestressed beams of large dimensions with high precision. These precast elements are indispensable for the development of transport infrastructures that require high strength and durability.
To produce these Box Girders with the required section, features and mechanical properties, the 2 Moldtech production lines use specific sets of moulds that define the shape of the parts.
Main features of the production lines
The main features of the production lines designed, manufactured and supplied by Moldtech can be summarised as follows:
- Hydraulic synchronised relaxation unit and pre-stressing equipment: this system allows the tensioning and de-tensioning of the cables used for the production of Box Girders, a fundamental feature to guarantee the structural strength of the elements produced and the safe operation of the lines. The de-tensioning unit allows the de-tensioning operation to be carried out automatically by means of a control system that ensures the controlled and synchronised movement of the de-tensioning cylinders.
- Vibration system: ensures the compaction of the concrete once it has been poured into the mould, improving the quality and durability of the elements produced. The system incorporates a centralised management system that allows the configuration of the system through a simple interface operated from a touch screen. The vibrators can be grouped so that they can be operated simultaneously from the remote control. Operators can disable or reassign different vibrators within each group to adjust the settings. All this allows an easy remote actuation, as well as a highly flexible system.
- Inner core collapse system: to improve the efficiency of the system, a hydraulically collapsible inner core has been incorporated to allow the demoulding of the parts, so that production can be carried out quickly and efficiently without damaging the precast elements, while minimising the required manpower.
- High-capacity tensioning system: the total tensioning capacity of this system reaches 1,900 tonnes, a critical requirement for large structures. This system includes several hydraulic cylinders.
- Accessories: cable launcher, lifting tool and lifting hook. These additional elements optimise material handling and guarantee safe operations of the system, ensuring efficient and safe production of the precast elements.
Impact of Moldtech’s Technology on the Alexandria Metro
Moldtech‘s contribution to the Metro project in Alexandria represents a significant contribution towards the modernisation of urban transports in Egypt. Thanks to its precast concrete solutions, a fast progress is being made in the construction of stations and other key structures for this project. The inclusion of elevated, station on the ground and underground stations minimises the impact on the densely populated urban areas, as these ones, while the design of underground tunnels in future phases will allow to get a great speed of operation, making the metro a viable and preferable alternative for daily use.
Such solutions reflect Moldtech‘s commitment, not only to quality and innovation, but also to sustainability and efficiency in urban infrastructure projects. With this collaboration, Moldtech and its client are marking a significant breakthrough in infrastructure construction in Egypt, setting a standard of excellence that can be served as a reference for future developments in the country and in the region.
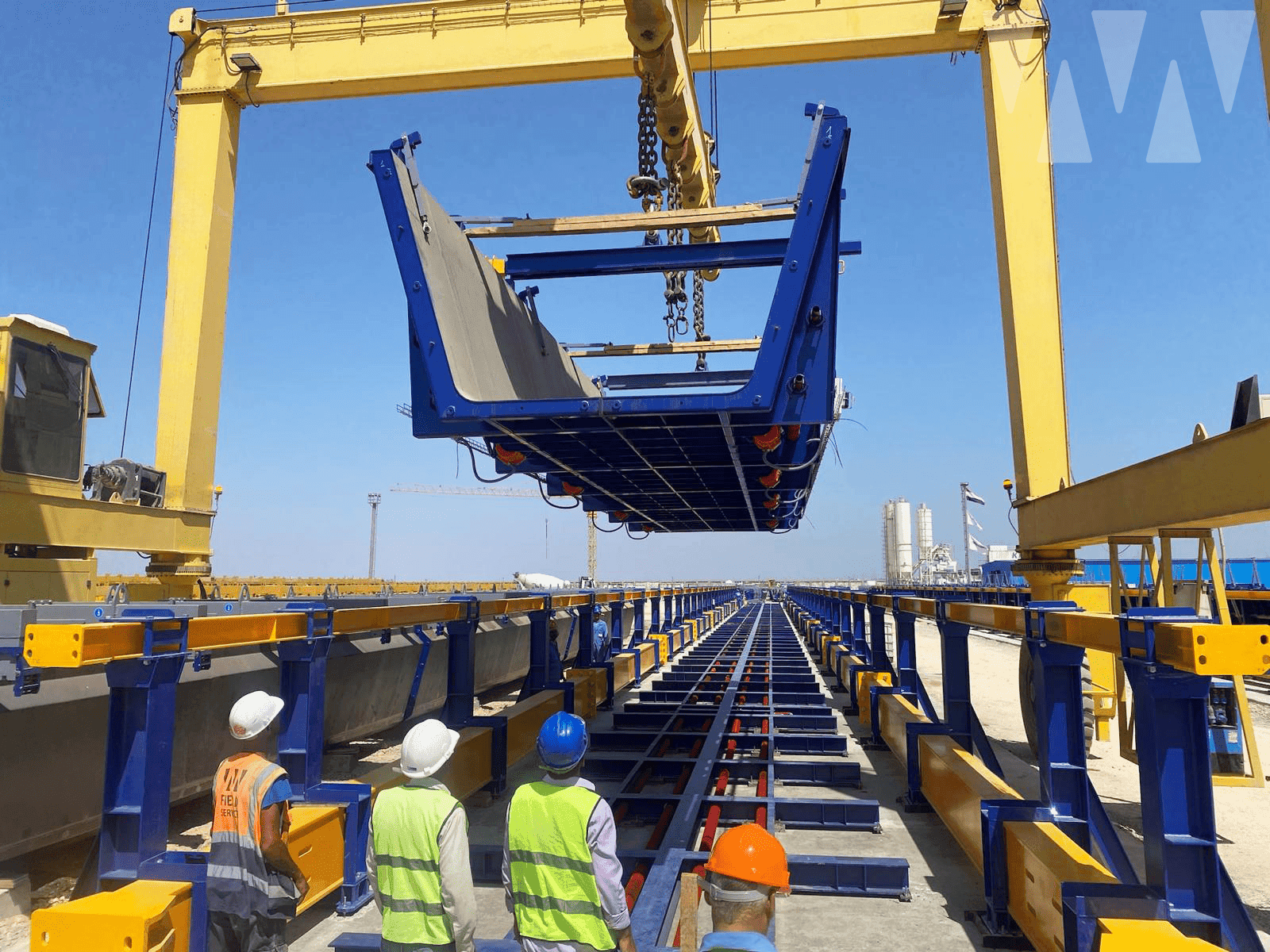
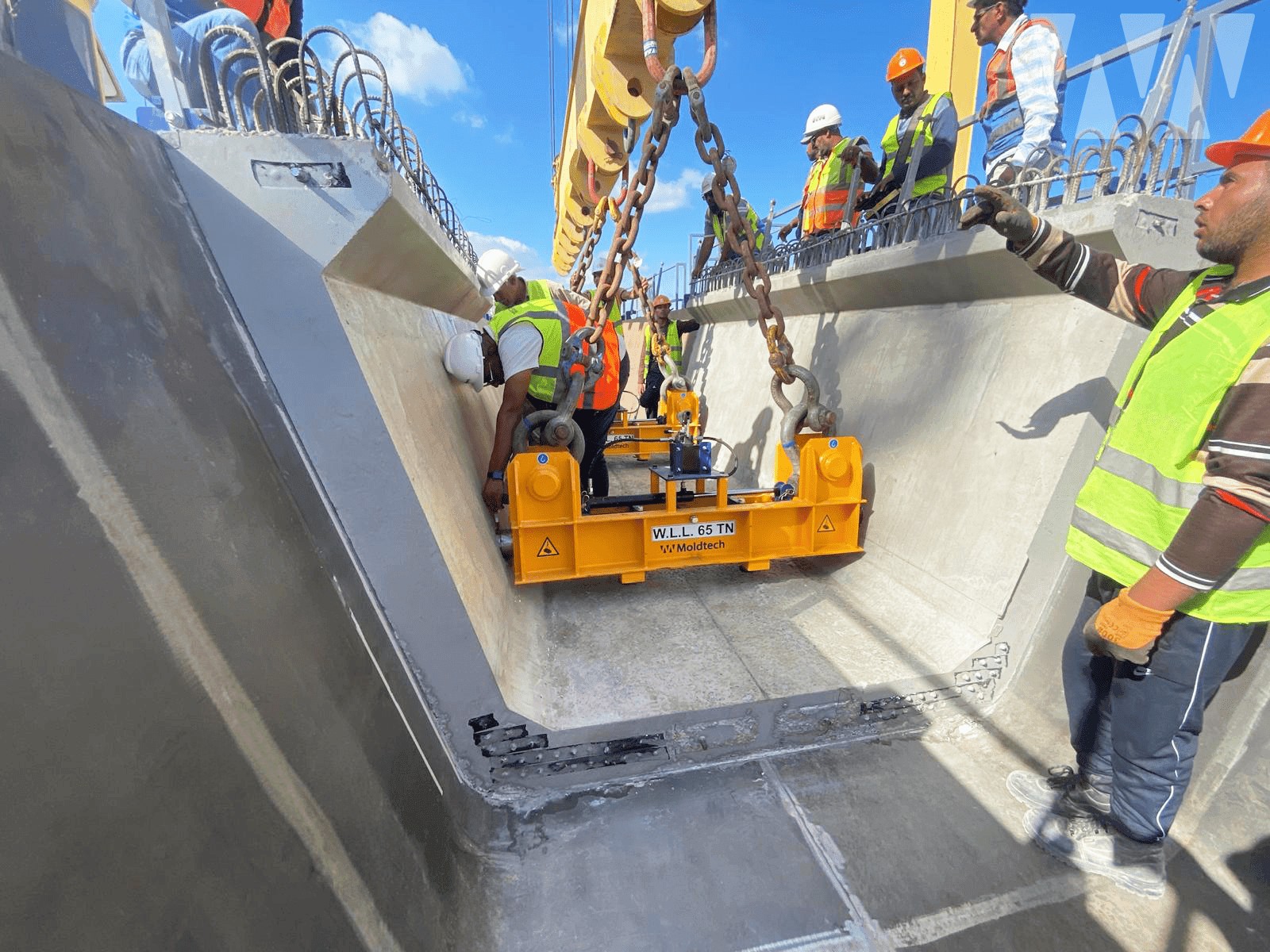
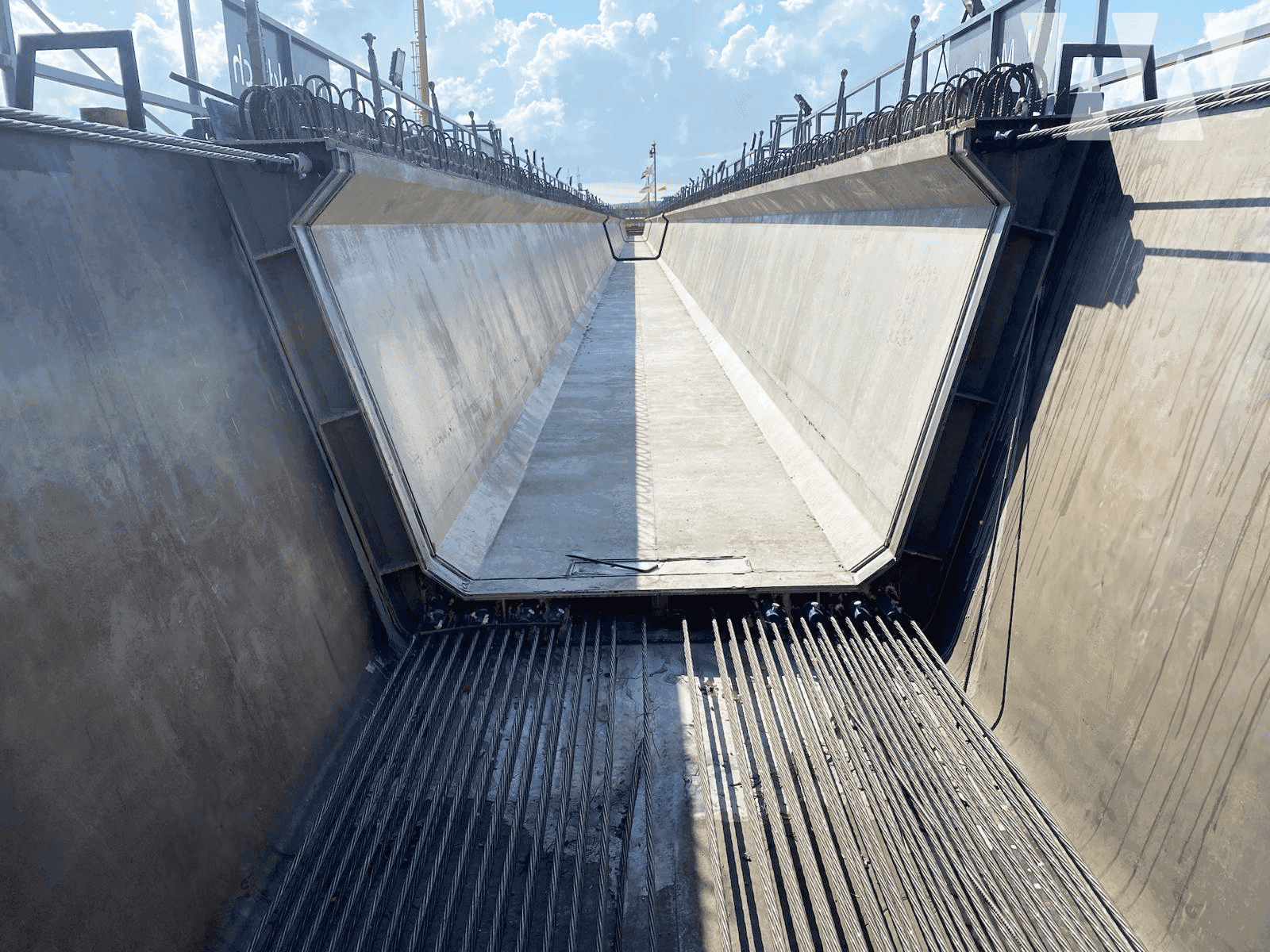
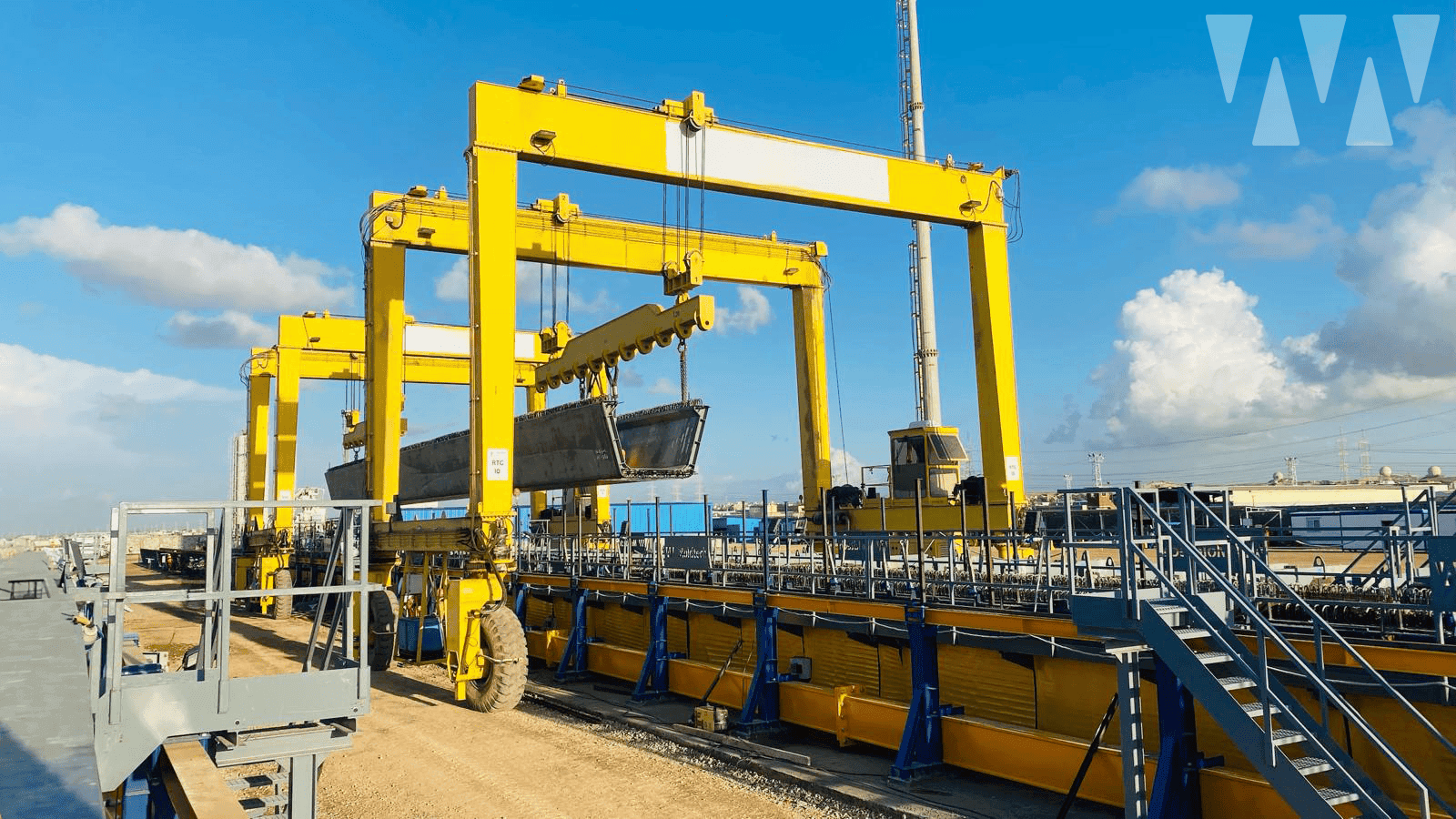
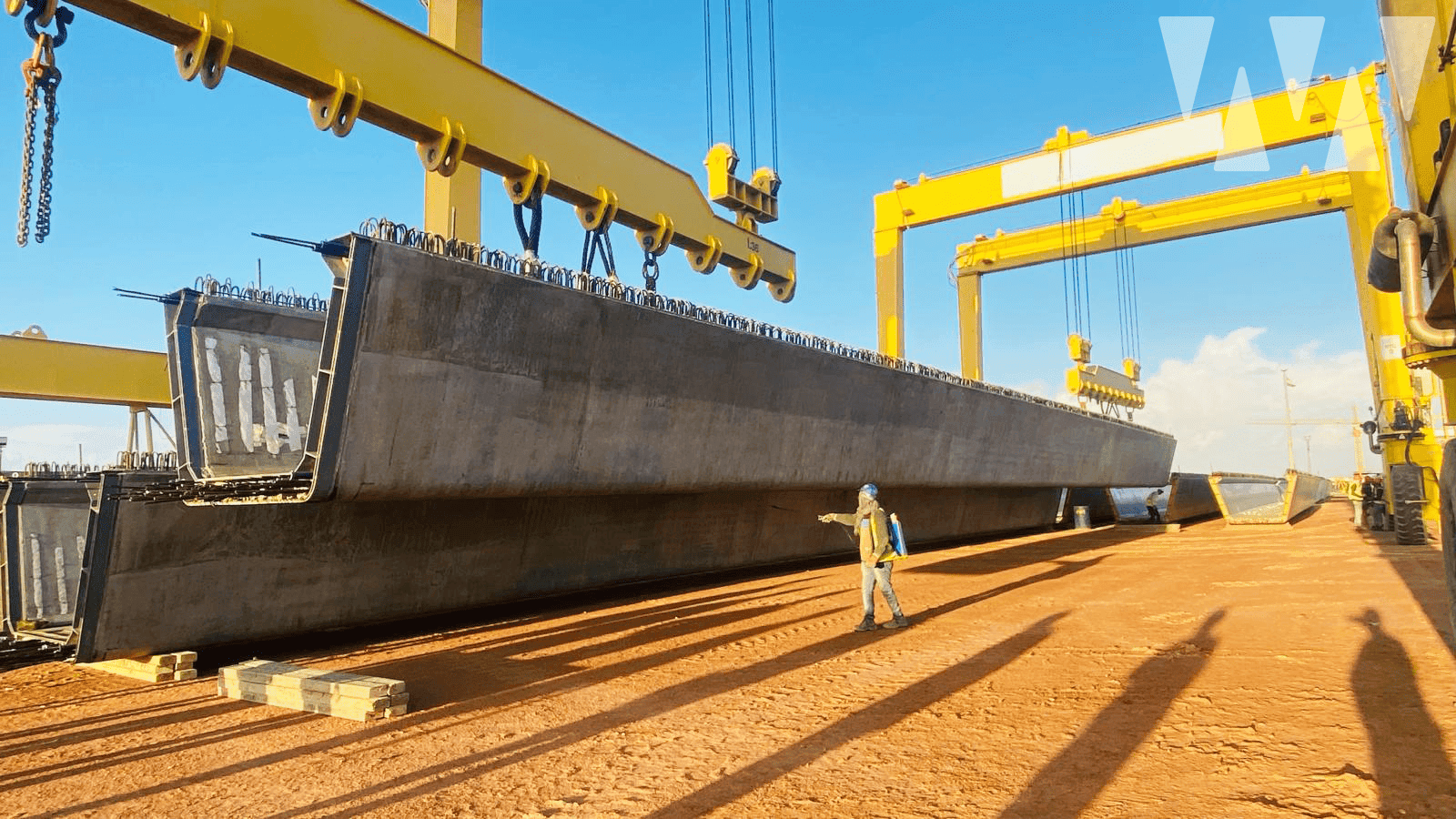
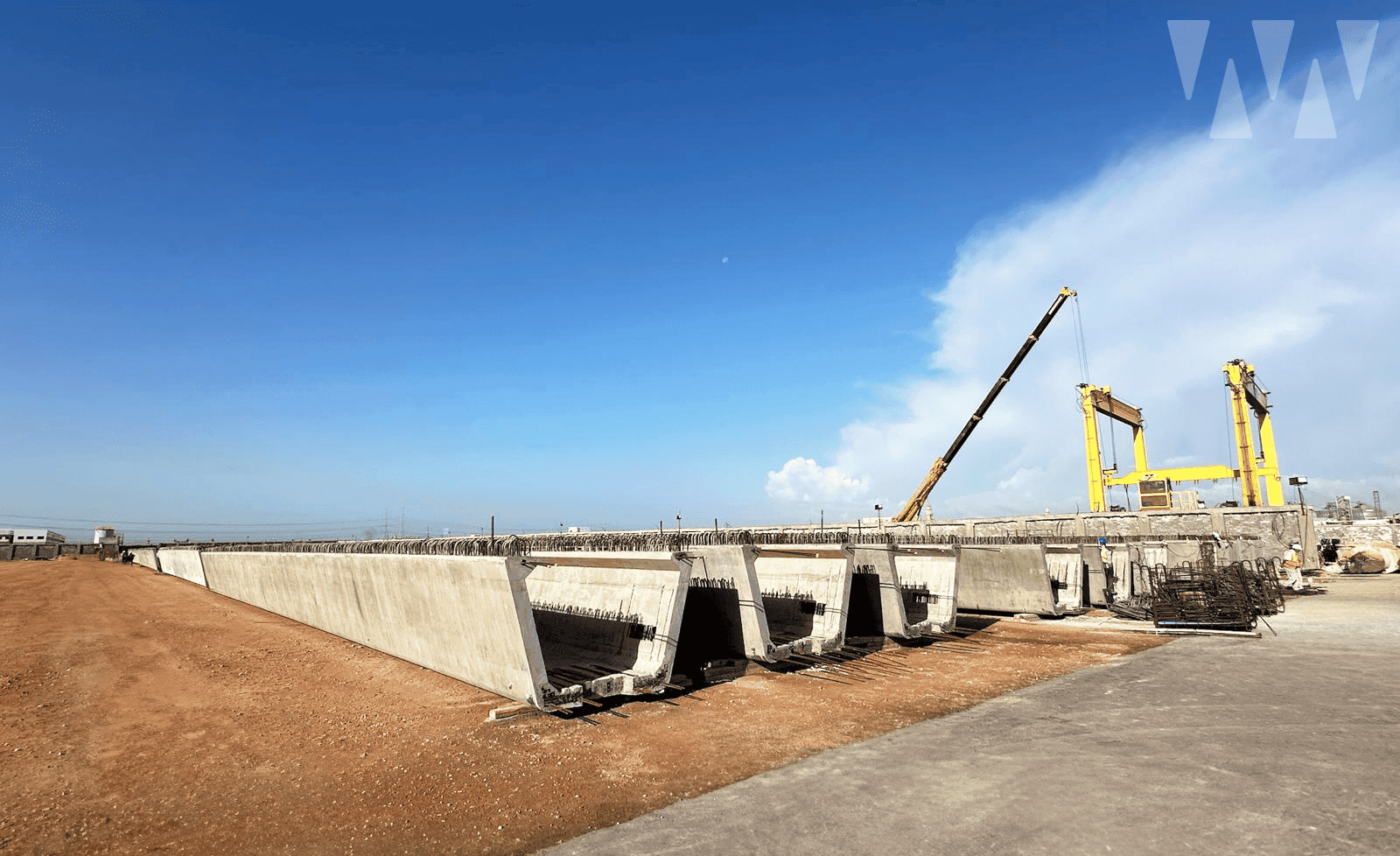
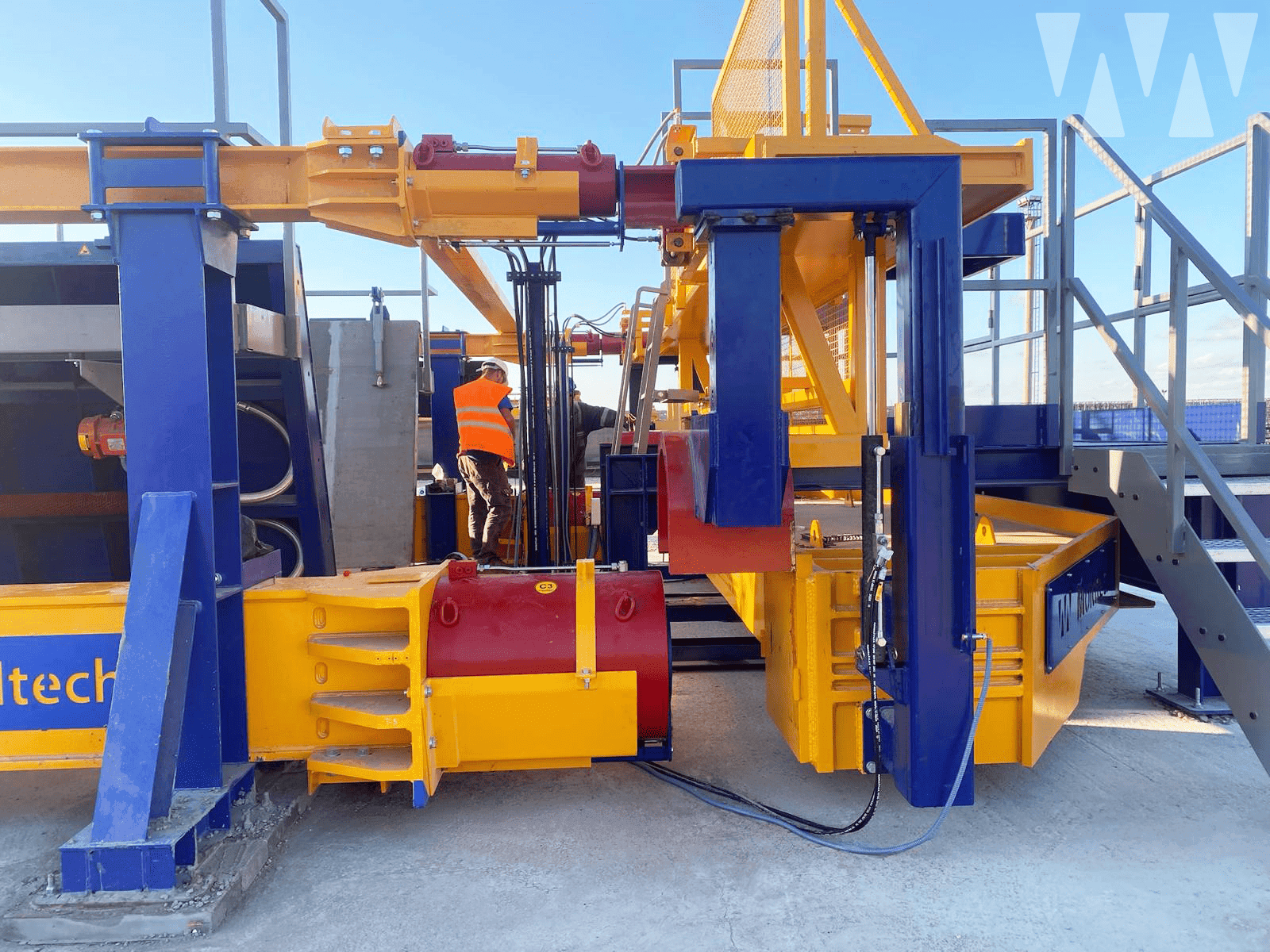