Moldtech, a global leader in precast concrete solutions, reinforces its position in international markets with a new shipment of a 400 tones TT mould, to an outstanding project.
Moldtech designed 400 tones self-reacting mould with hydraulic opening for the manufacture of prestressed concrete TT slabs with variable sections. This equipment allows the production of elements with a maximum length of 60 meters, rib heights ranging between 620 mm and 1,200 mm, and a width of 2.6 meters. A notable feature is the regulation of the central body of the slab to adapt to different regulations in addition to its adjustable bottom height regulation, which facilitates the adjustment of the section of the pieces according to the specific needs of the project.
The self-reacting mould is made up of an active head and a passive head, located at the ends of a set of cores, which together with the set of side moulds shape the elements to be manufactured. The installation requires the use of the supplied hydraulic power unit and electrical panel for the opening and closing maneuvers of the side moulds, as well as the detensioning power unit to operate the relaxation cylinders.
The system is prepared to work with cable tensioning and relaxation equipment, supporting a maximum tensioning capacity of 400 tons. This prestressing capacity provides a greater length of elements to be manufactured, making them ideal for use in the construction of industrial and commercial buildings.
Besides, the mould includes a vibration system for compacting the concrete, composed of a series of vibrators, installed on the side moulds. This system eliminates air from the concrete, increasing the resistance of the element and allowing the use of mixtures with a lower proportion of water, which accelerates the curing process and, consequently, increases productivity.
Another advantage of the self-reacting design of the mould is that it integrates in itself the heads that support the tensioning and detensioning operations, simplifying its installation and dismantling, and facilitating its mobility to different production locations, allowing manufacturing directly on the job site that significantly reducing costs and the need for transportation of precast elements.
It also includes a magnet fixing system, a key technology in the precast concrete industry that secures formwork firmly and safely without the need for drilling or welding. It uses high-performance neodymium magnets, guaranteeing durability and resistance, as well as facilitating assembly and disassembly.
Main advantages:
- Agility: Reduces installation and disassembly times.
- Flexibilidad: Allows quick adjustments for different designs.
- Quality: Improves the finish and precision of precast elements.
This system is ideal for optimizing the production of concrete elements with high efficiency and reliability, offering versatile and durable solutions.
Tu summarize everything up the Moldtech mould for TT slab offers an efficient and versatile solution for the production of prestressed concrete TT slabs, adapting to various project specifications and guaranteeing high quality and resistance in the manufactured elements.
This advancement reaffirms the company’s commitment to technological innovation and meeting the specific needs of its clinets around the world.
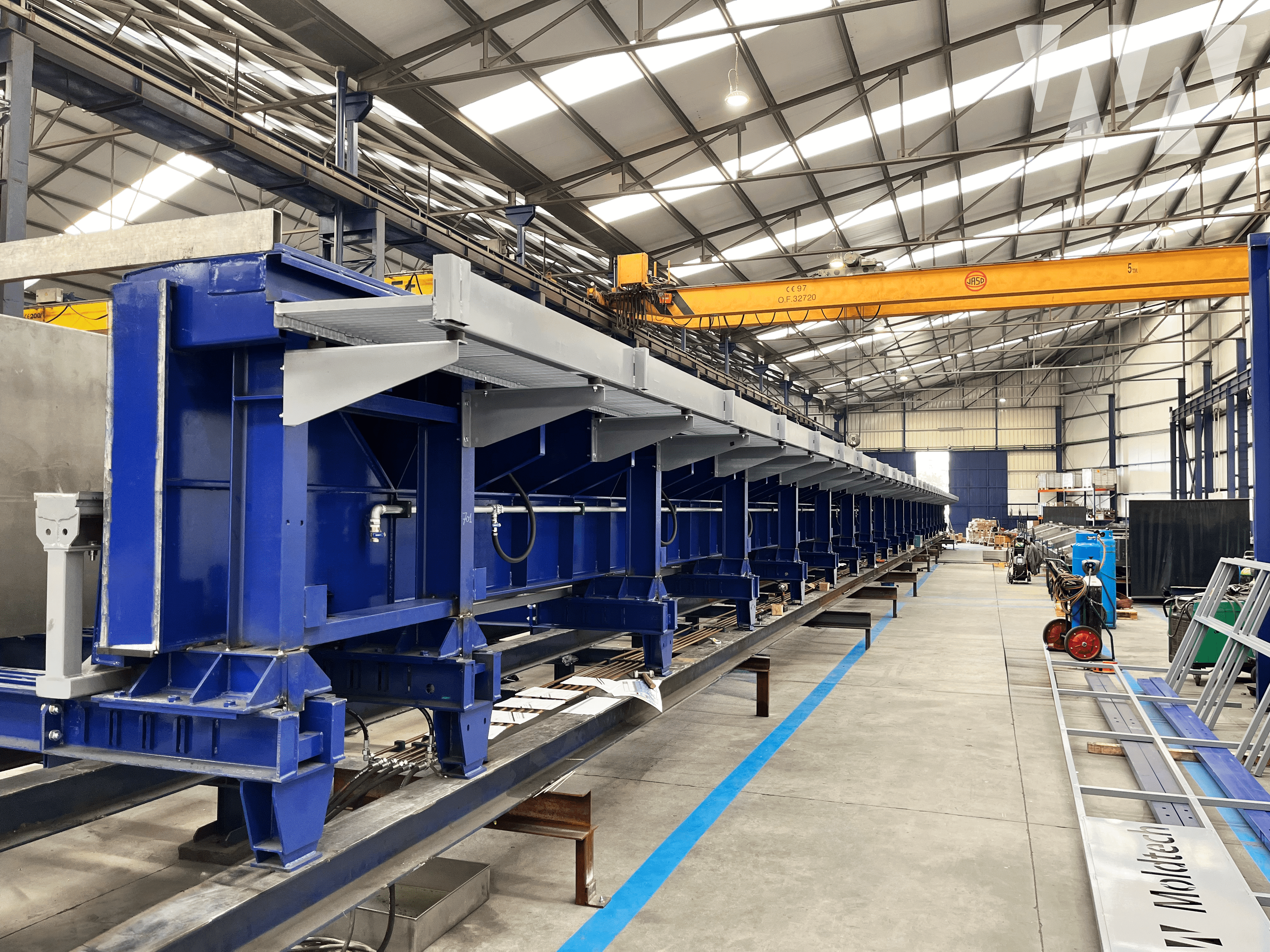
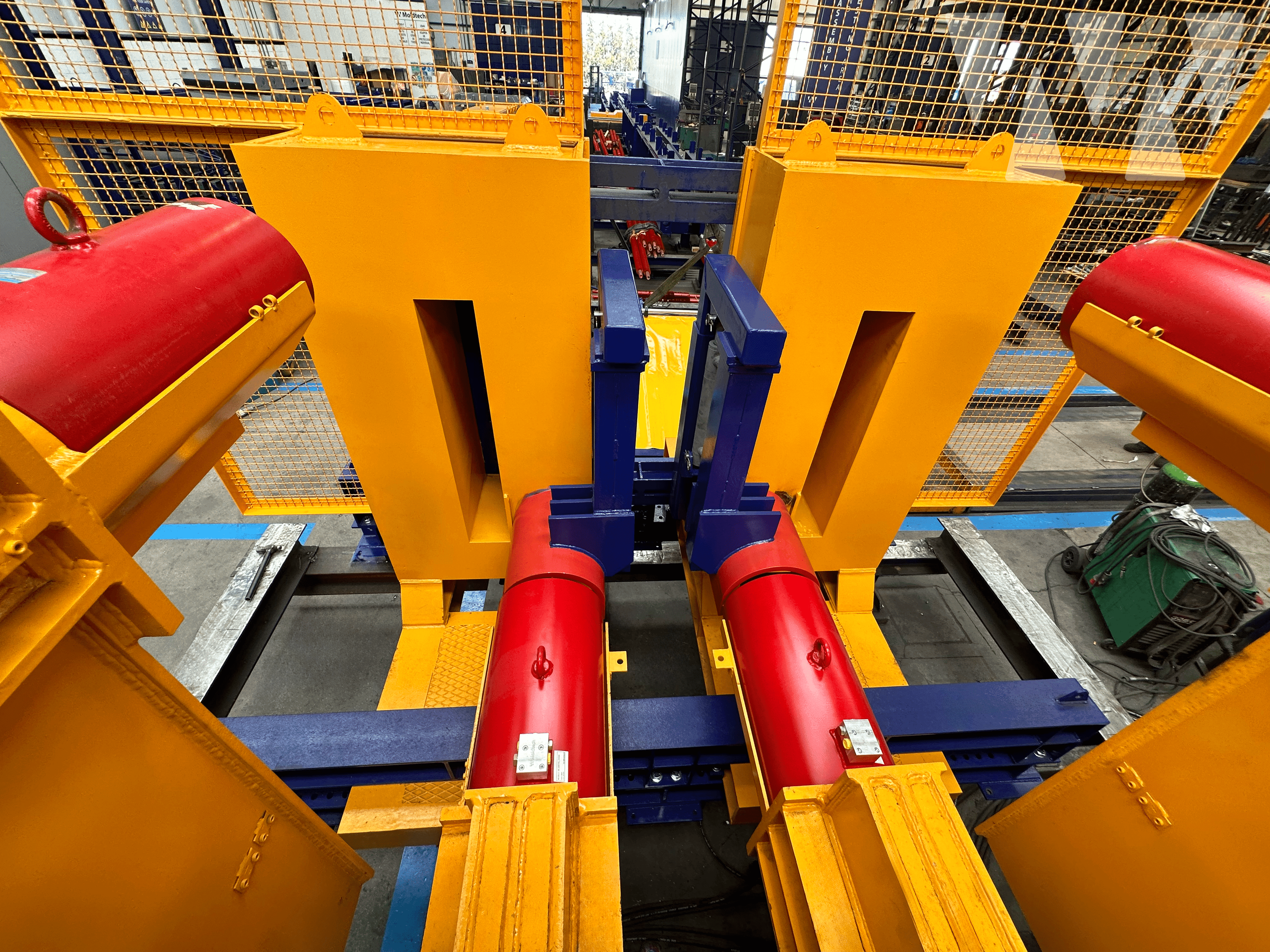
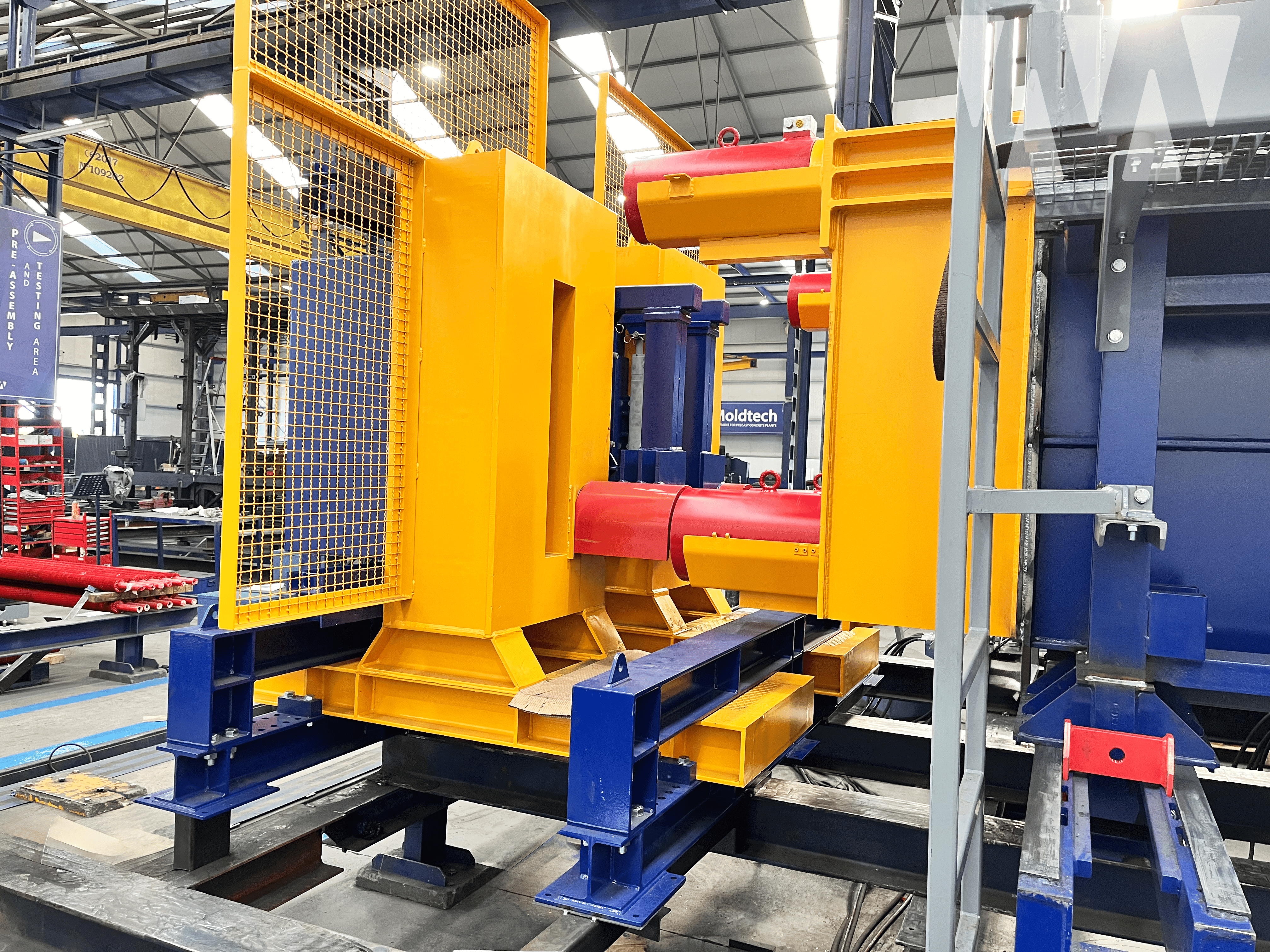
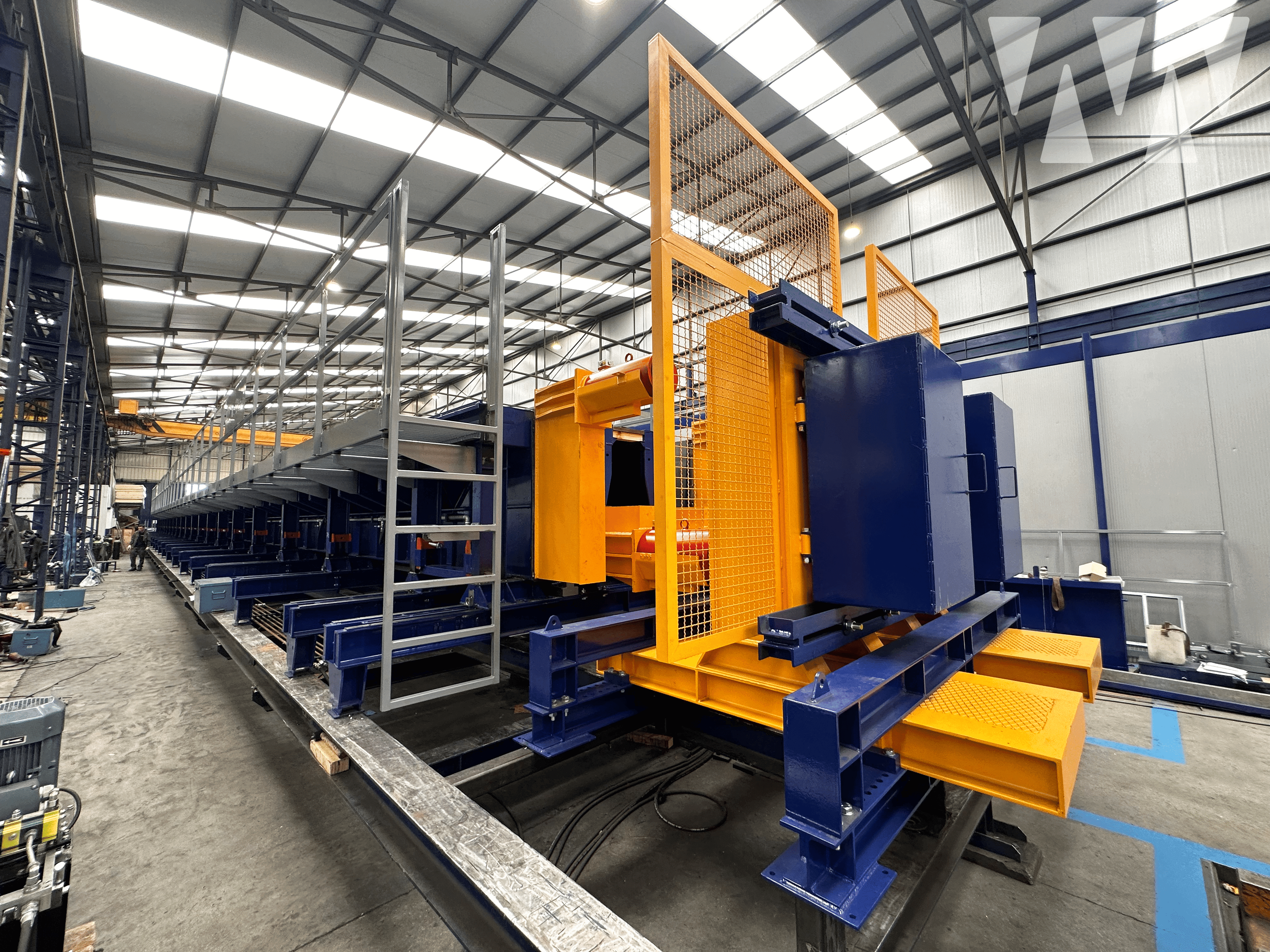
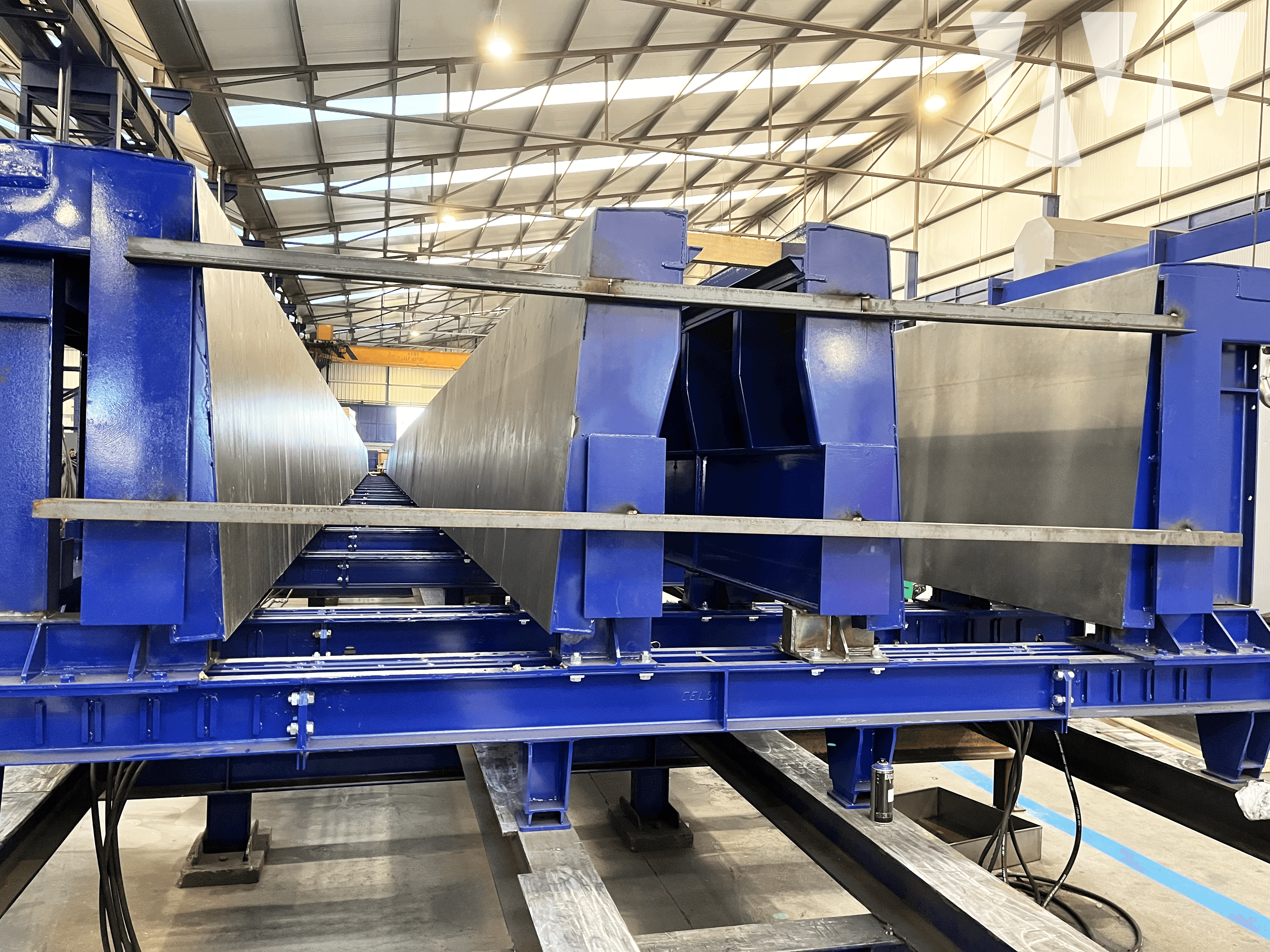

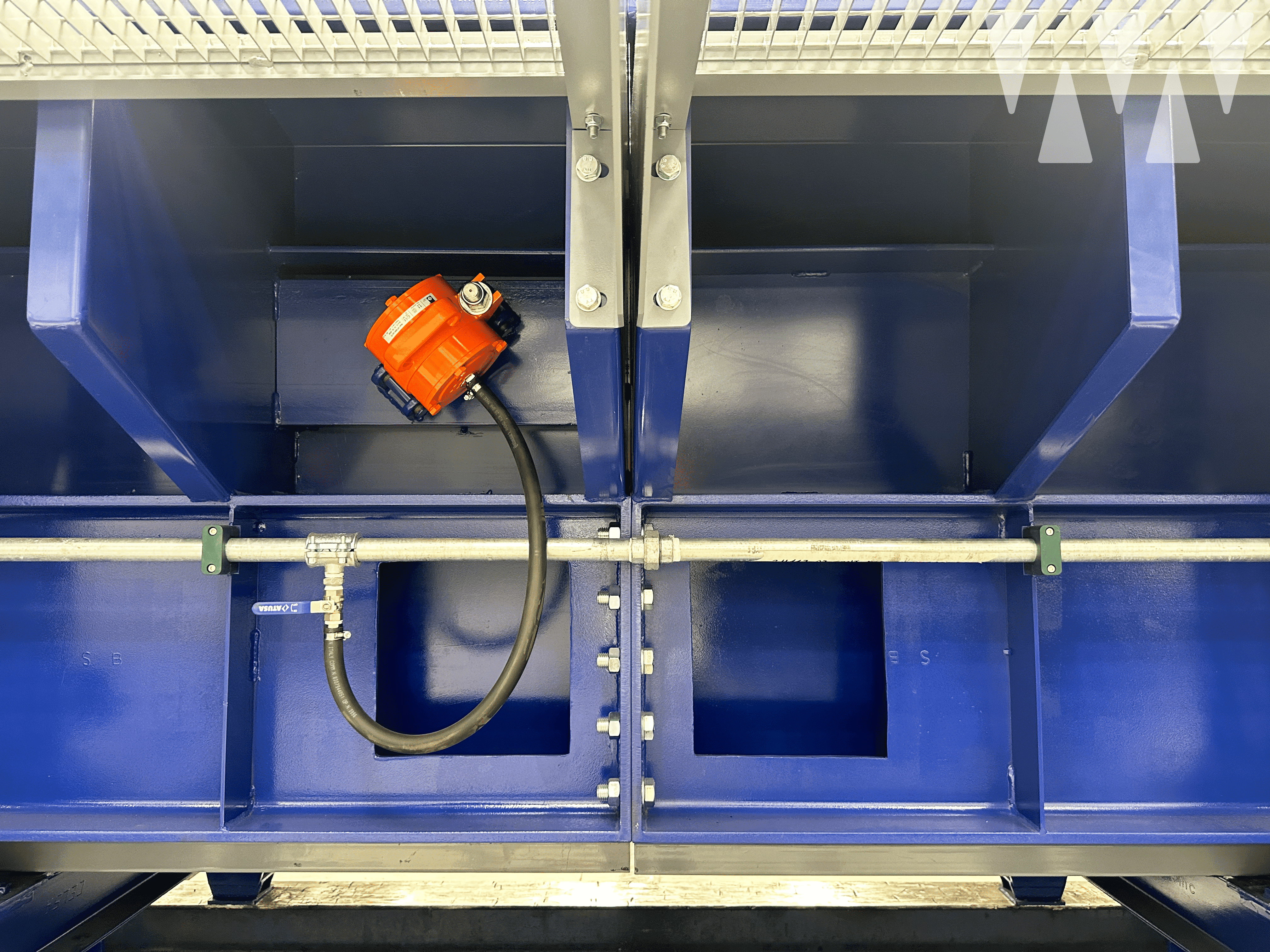