Innovation and collaboration: the fusion of cutting-edge technology and local expertise transforms precast concrete in Hungary.
In a strategic move that promises to transform the construction landscape, Moldtech announces its foray into the competitive Hungarian market. The company, recognized for its leadership in technology and complete equipment for precast concrete construction, aims to consolidate its presence in a region that has emerged as a true epicentre of innovation in this sector.
The Hungarian precast concrete construction market is characterised by sustained growth, driven by infrastructure investments and large-scale urban developments. The modernisation of construction techniques, together with the implementation of regulations that favour efficiency and sustainability, have made Hungary fertile ground for the adoption of new technologies. Local and international companies are increasingly open to integrating solutions that optimise the quality and durability of structures, which positions the country as a key market for industry leaders such as Moldtech.
This new stage in Moldtech’s international strategy underlines the dynamism and opportunities present in the Hungarian construction industry. With this move, the synergy between cutting-edge technology and Hungary’s strong precast concrete market is expected to open the door to new projects.
Collaboration with ÉPI: quality and innovation in prefabrication
Moldtech’s partner company, Épszerk – Pannónia Invest Construction Ltd. (ÉPI), has established itself as one of the leading construction companies in Hungary with over 30 years of experience. Specialising in monolithic reinforced concrete structures, it has been involved in hundreds of projects ranging from residential and commercial buildings to highly demanding industrial infrastructures. Its growth has been marked by innovation, certified quality and a network of reliable subcontractors, which has allowed it to expand its activities both nationally and internationally in countries such as France, Austria and Romania. With its own precast concrete plant and a constant commitment to modernisation, ÉPI continues to evolve to respond to market needs with cutting-edge construction solutions.
Japport Ákos, ÉPI’s precast and technology development engineer, highlights the importance of quality in the manufacture of precast elements and its impact on the success of projects:
“Our mission is to prioritize quality in the manufacturing of precast elements, ensuring the success and durability of construction projects. We offer a diverse product portfolio, including solid and sandwich walls, linear structures (columns, beams) and a wide range of tailored-made orders. These include decorative roof elements, street furniture and components for landscape and garden architecture. Through our commitment to excellence, we strive to deliver innovative and reliable solutions for every project.”
One of the company’s most recent projects, in collaboration with Moldtech, went off without a hitch. Ákos emphasises the efficiency of the process and the professionalism of the team:
“From the initial quote to placing the order, detailing every aspect, arranging the delivery and finally completing the assembly, everything was handled efficiently and effortlessly! The entire Moldtech team was a pleasure to work with as they were professional, helpful and flexible throughout the entire process.”.
Advanced technology in the precast process
The delivery consists of two tilting tables, designed to produce precast non-prestressed concrete panels. These panels can reach a maximum length of 13.5 m, a height of 4.5 m and have a variable thickness between 80 and 450 mm. Each table is supplied with an electric vibration system.
The tilting table is made up of a fixed frame, with supports anchored to the foundation slab, and a tilting board that allows a tilt of up to 74º. This creates a production line 13.5 m long by 4.5 m wide. It also includes a lower longitudinal side, folding transverse sides and a magnetic formwork system as the upper side; all of them mechanically adjustable in height to manufacture pieces of various thicknesses (between 80 and 450 mm).
The tilting process is carried out by hydraulic cylinders, which are activated by a hydraulic unit and a main control cabinet included in the equipment supply. The table has a total of 14 strategically distributed vibrators, connected to the supplied concentration box. The magnetic formwork is fixed by a magnet system, and the table’s anchoring structure is prepared for the correct placement of these.
This first supply represents the beginning of what we hope will be a long-lasting working relationship.
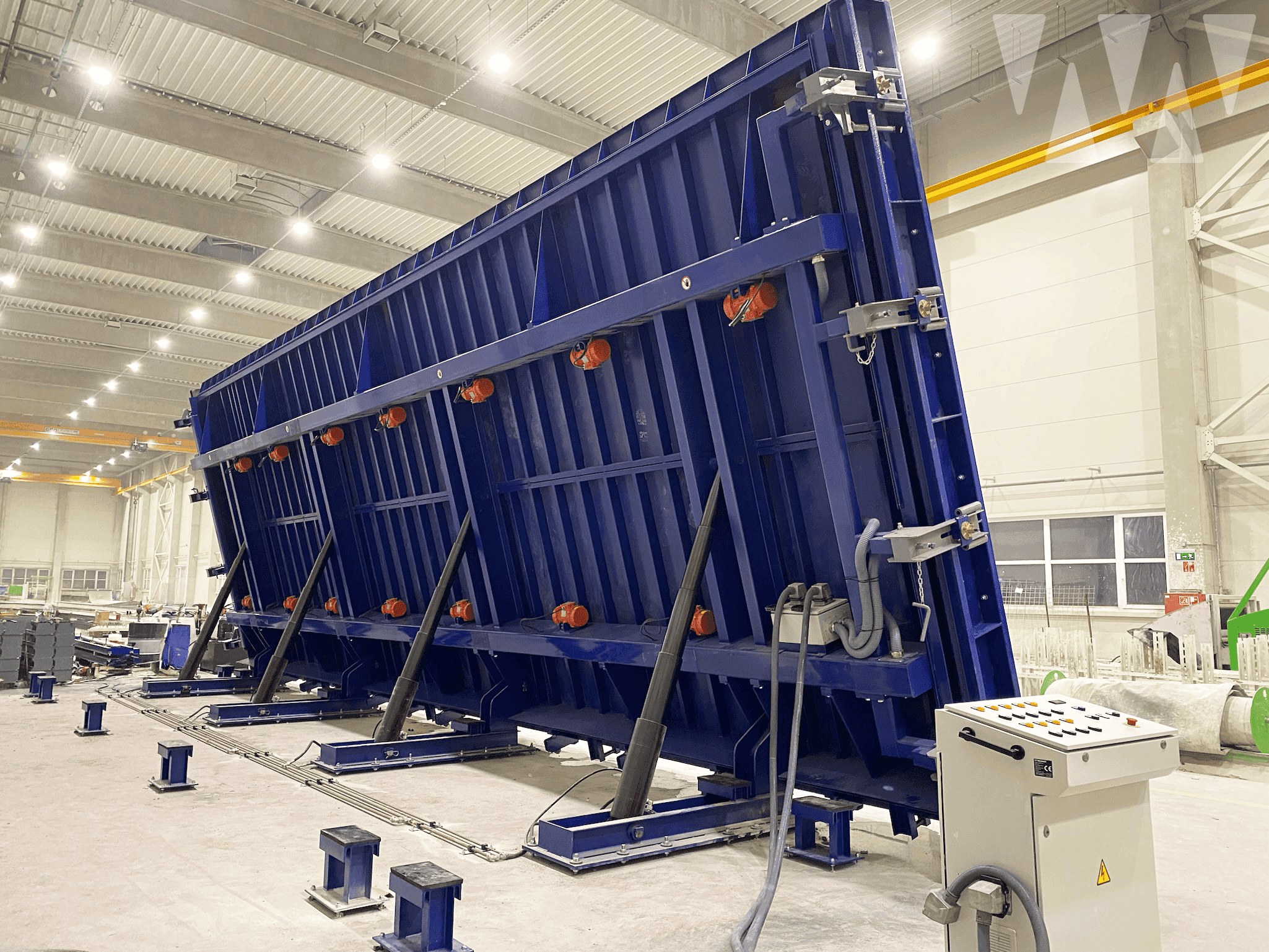
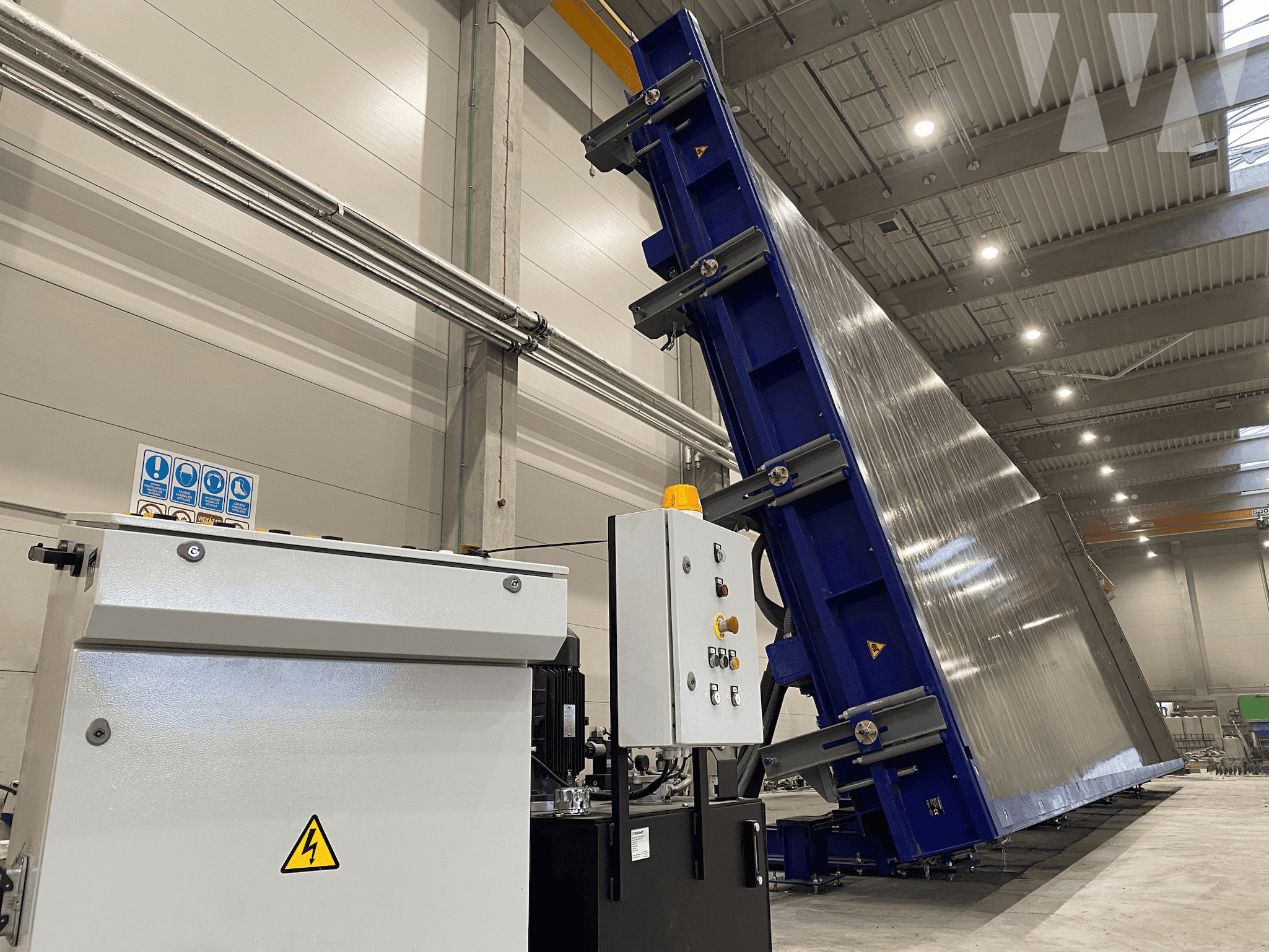
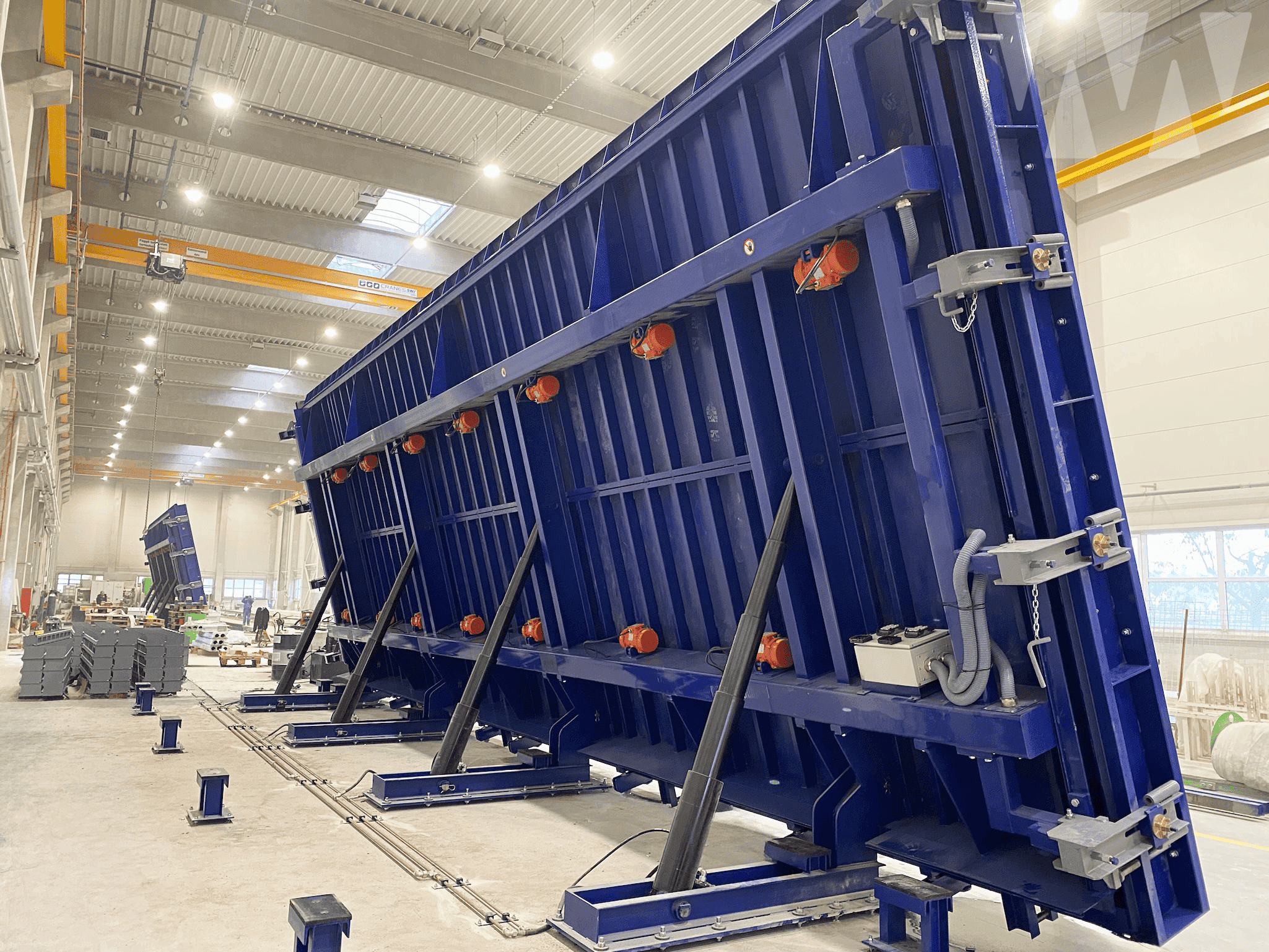
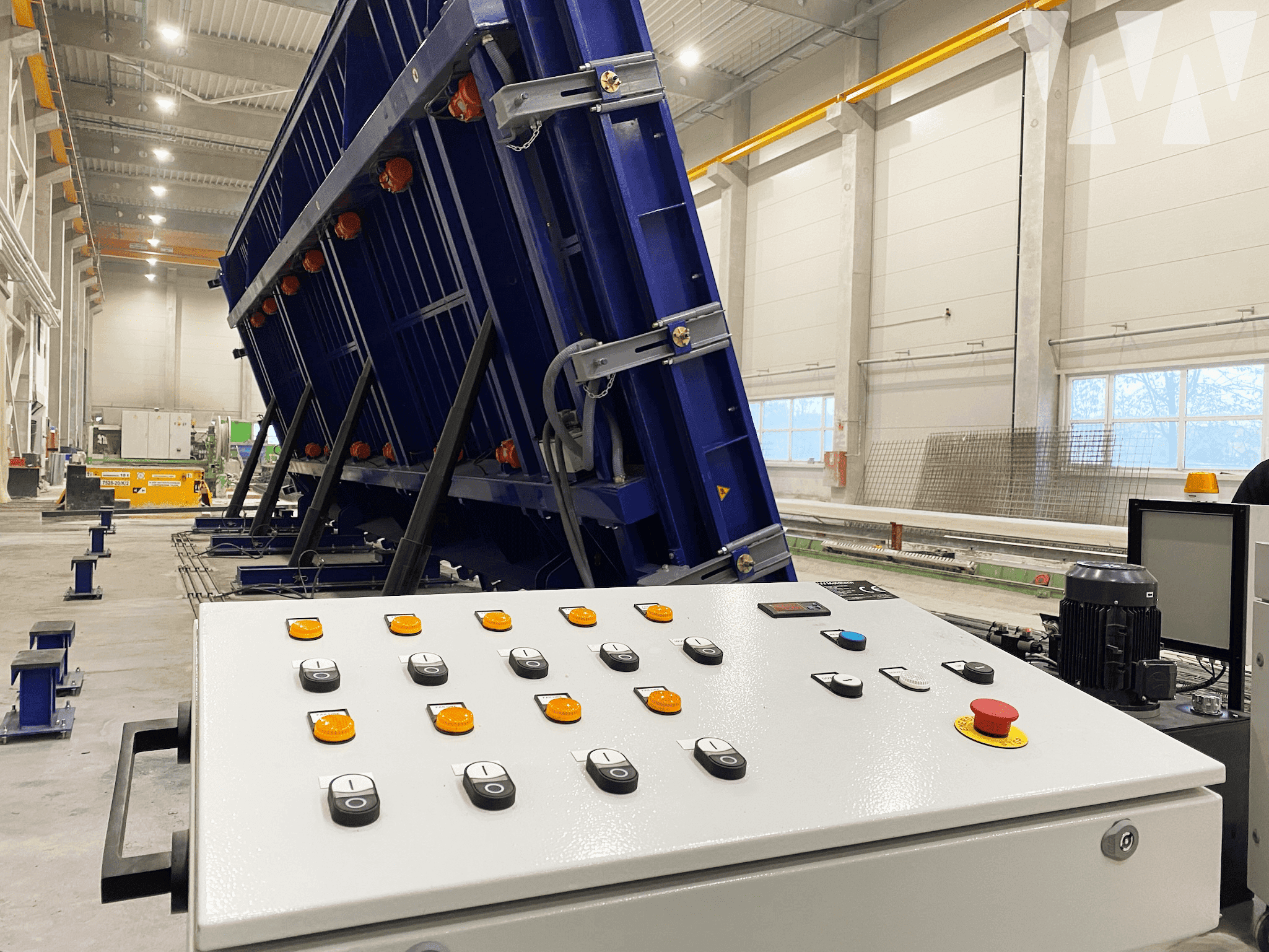
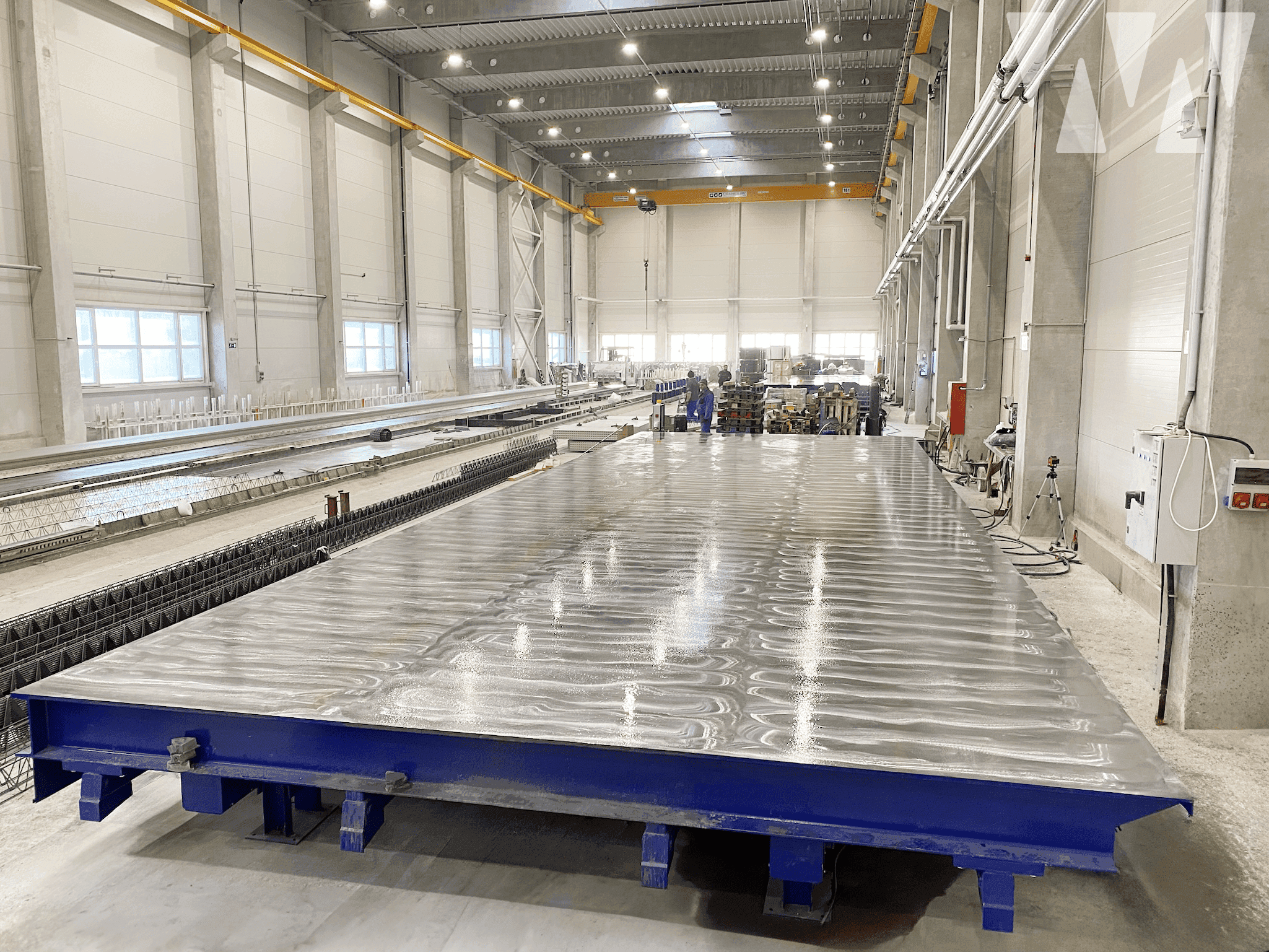
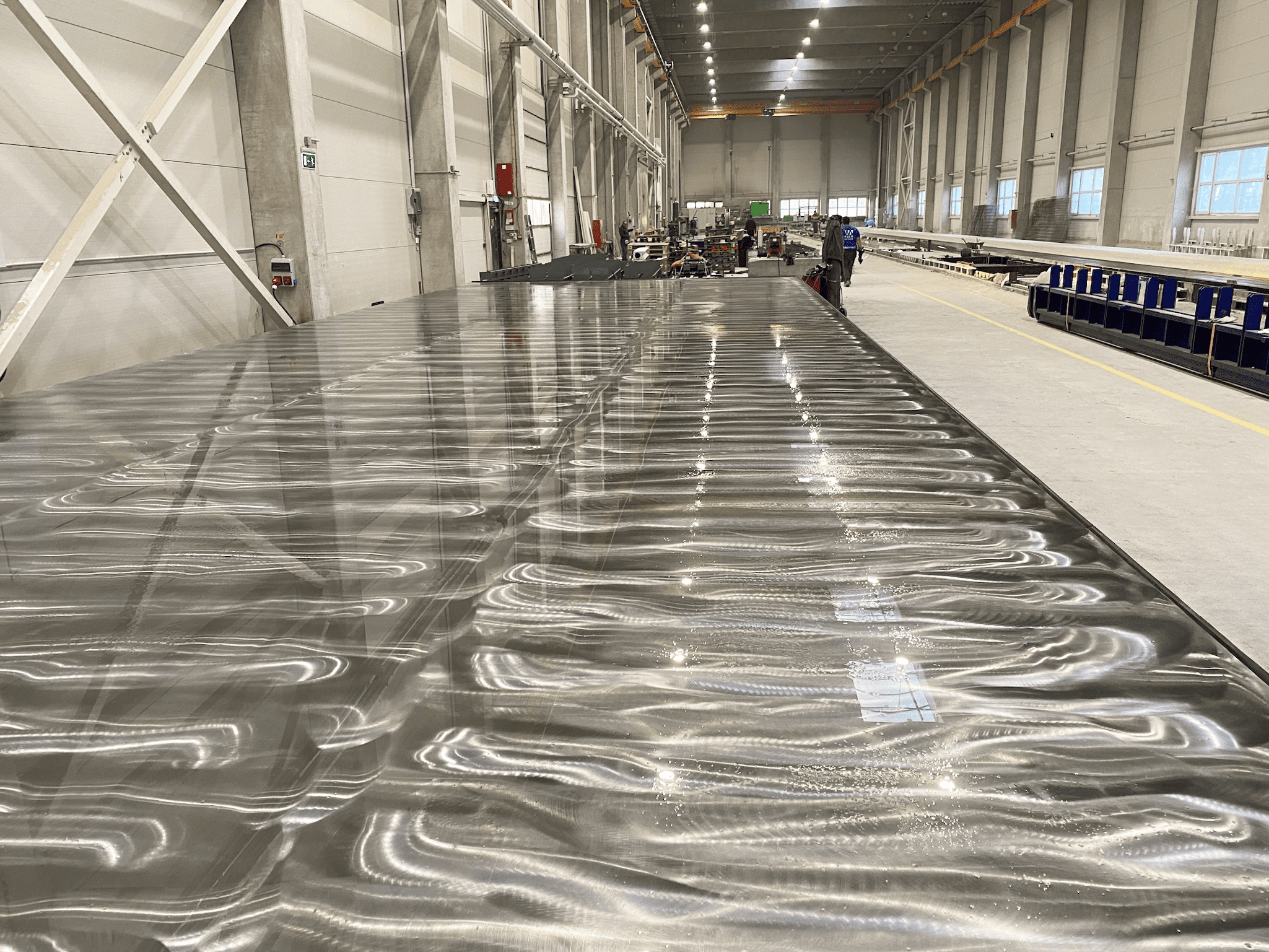
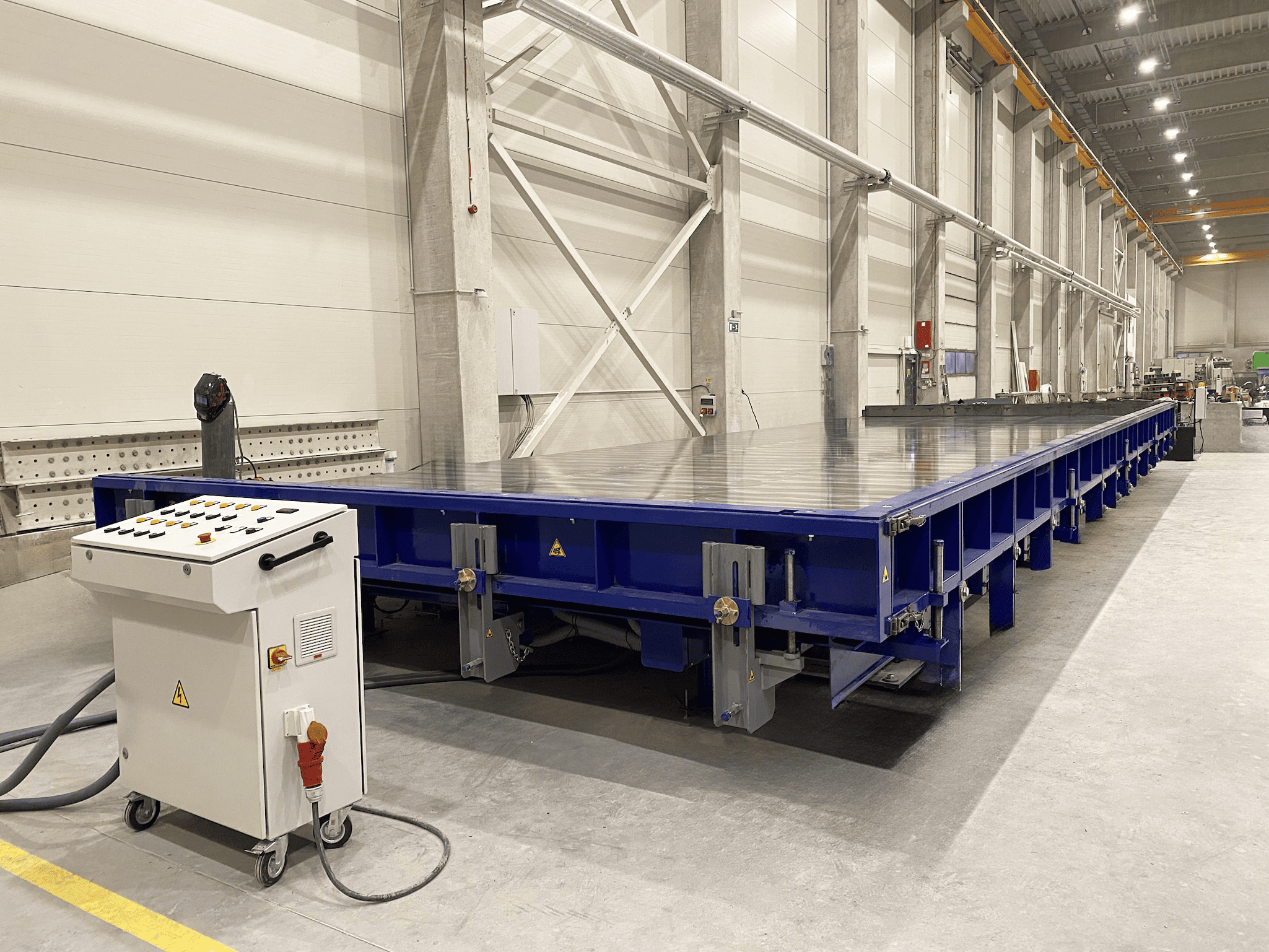
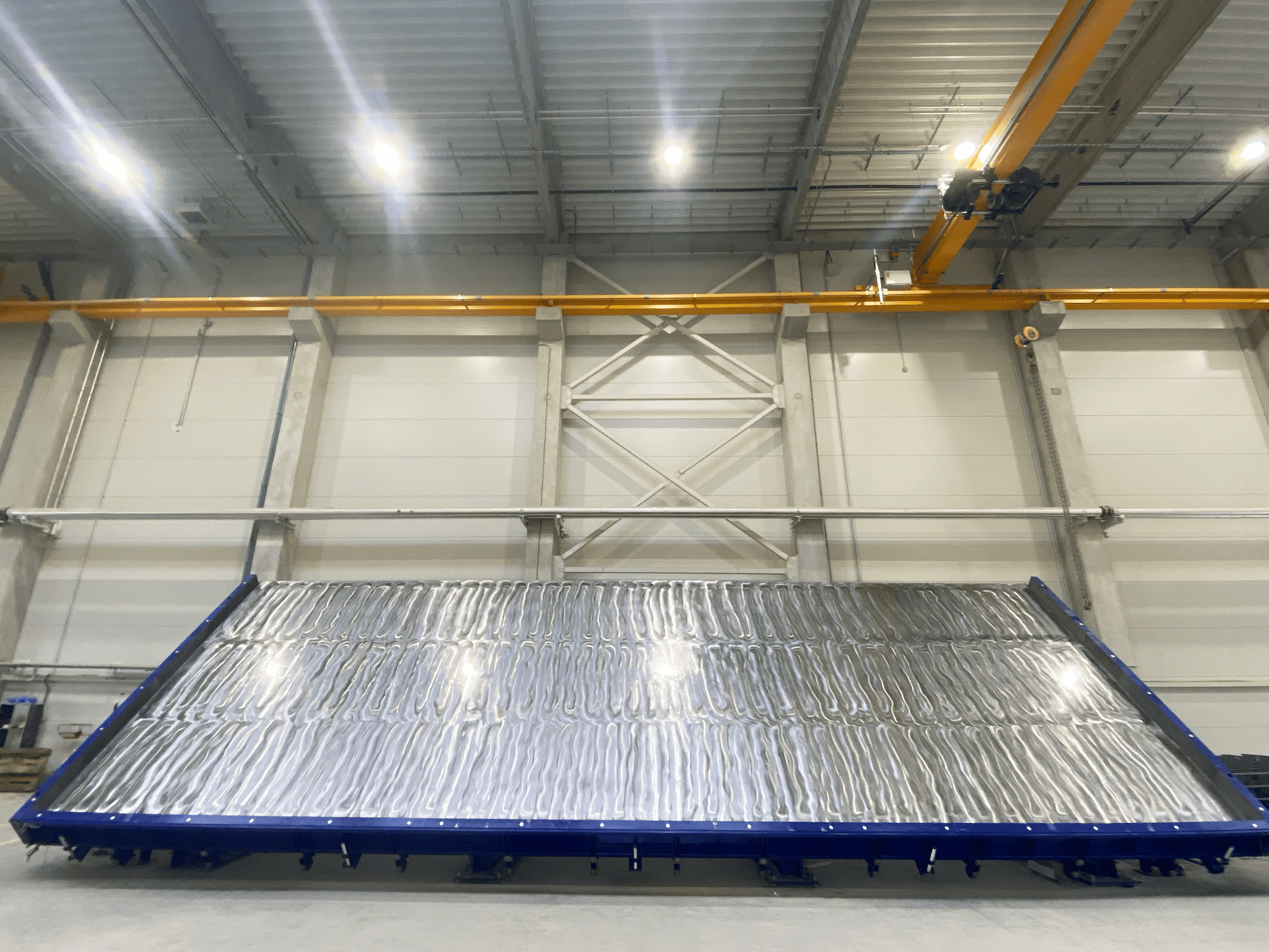