Moldtech presents a fully automated circulation line to carry out finishing work on 3D precast bathroom modules (“PBU”).
P.B.U. (Prefabricated Bathroom Units) are one of the 3D elements which nowadays are becoming increasingly popular in the precast world. These units allow to finish the complete bathroom in a factory environment. And then the completely finished unit is shipped to the construction site where it is “inserted” into the building. This methodology allows for increased quality control and more reliable production schedules while decreasing the demand for manpower at the building site.
The 3D moulds allow the client to precast the walls and floor of the bathroom as a monolithic structure. Further, the casted element is turned 180º. Additionally, after turning, the casted element is placed on a pallet and transferred into the “finishing” factory. Inside this factory the casted element passes through a variety production bays where the element is finished in several steps involving waterproofing, laying of tiles, installation of fittings etc… This way the bathroom can be shipped to the construction site almost “ready to use”.
The automated system for moving the pallets which involved several longitudinal lines using traction wheels and a central shifter for moving the pallets from one line to the next. This moving system is completely automated allowing the client to program in advance the trajectory of the PBU. Furthermore, the program allows the assure traceability and to monitor production times at each finishing bay. One important aspect of the collaboration between Moldtech and its client was the ability to personalize the production line set-up to the exact requirements of the client. With this project Moldtech continues its path of innovation to develop the best technology for the precast industry.
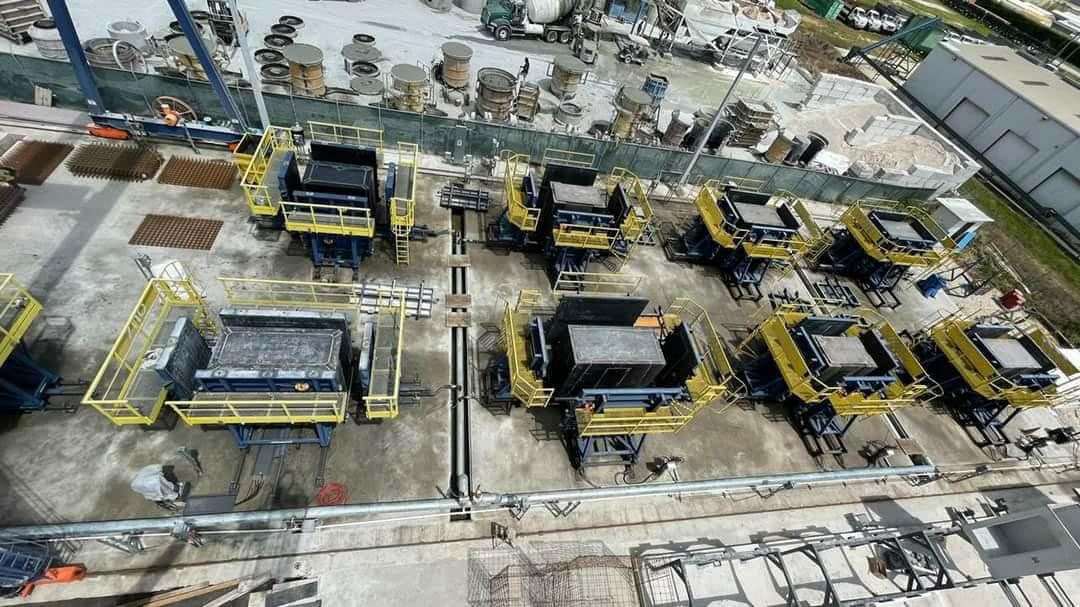
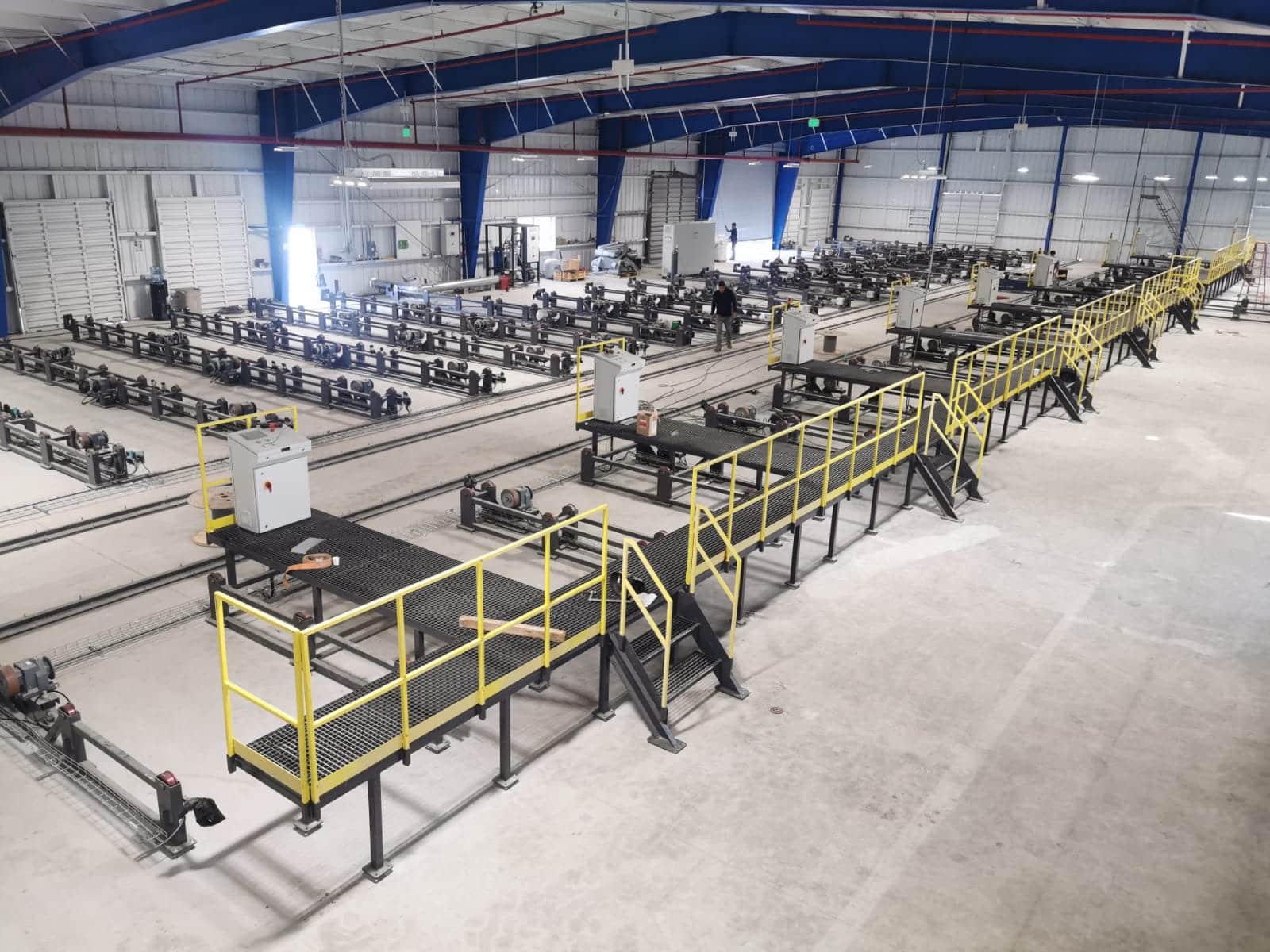
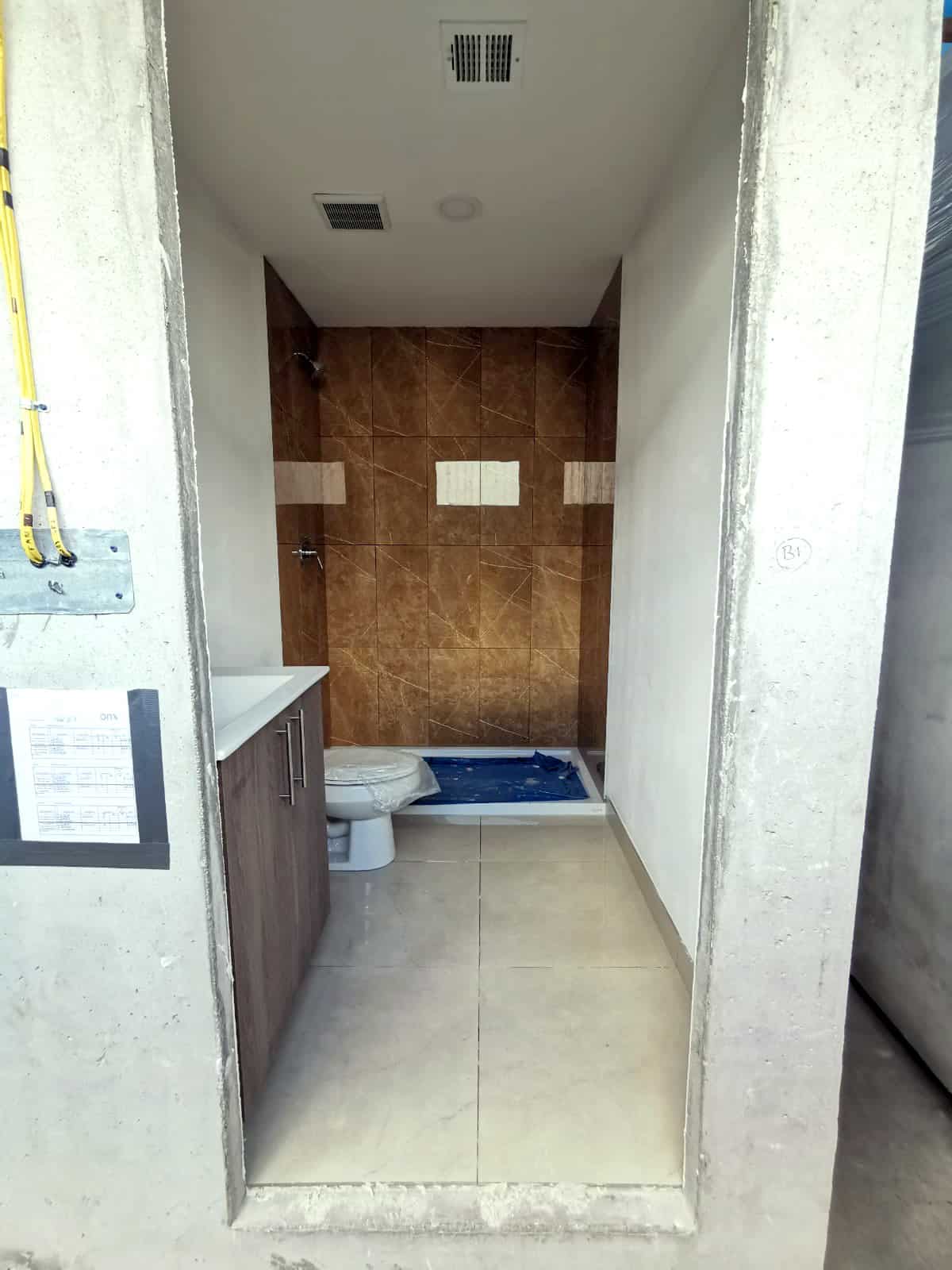
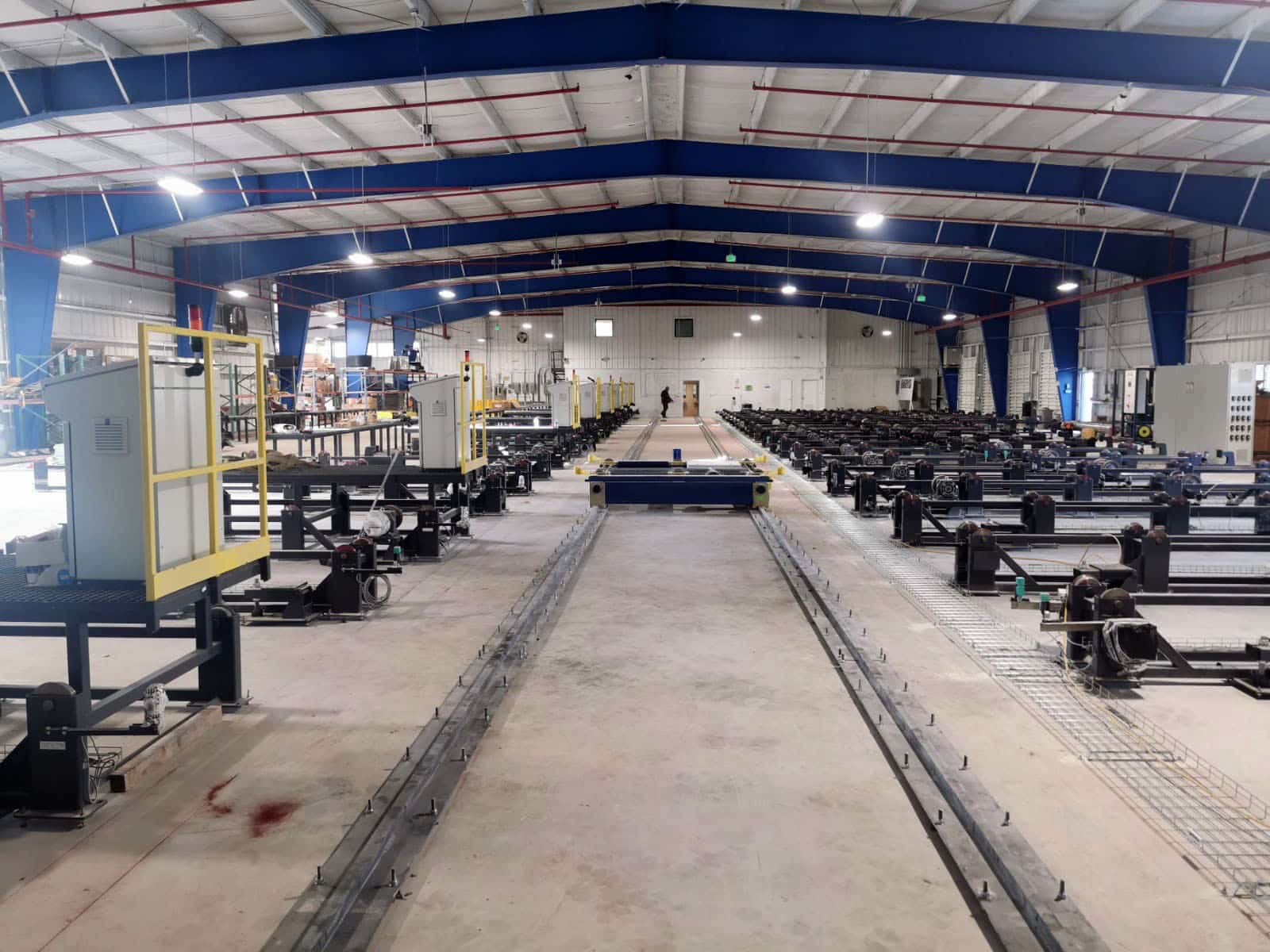
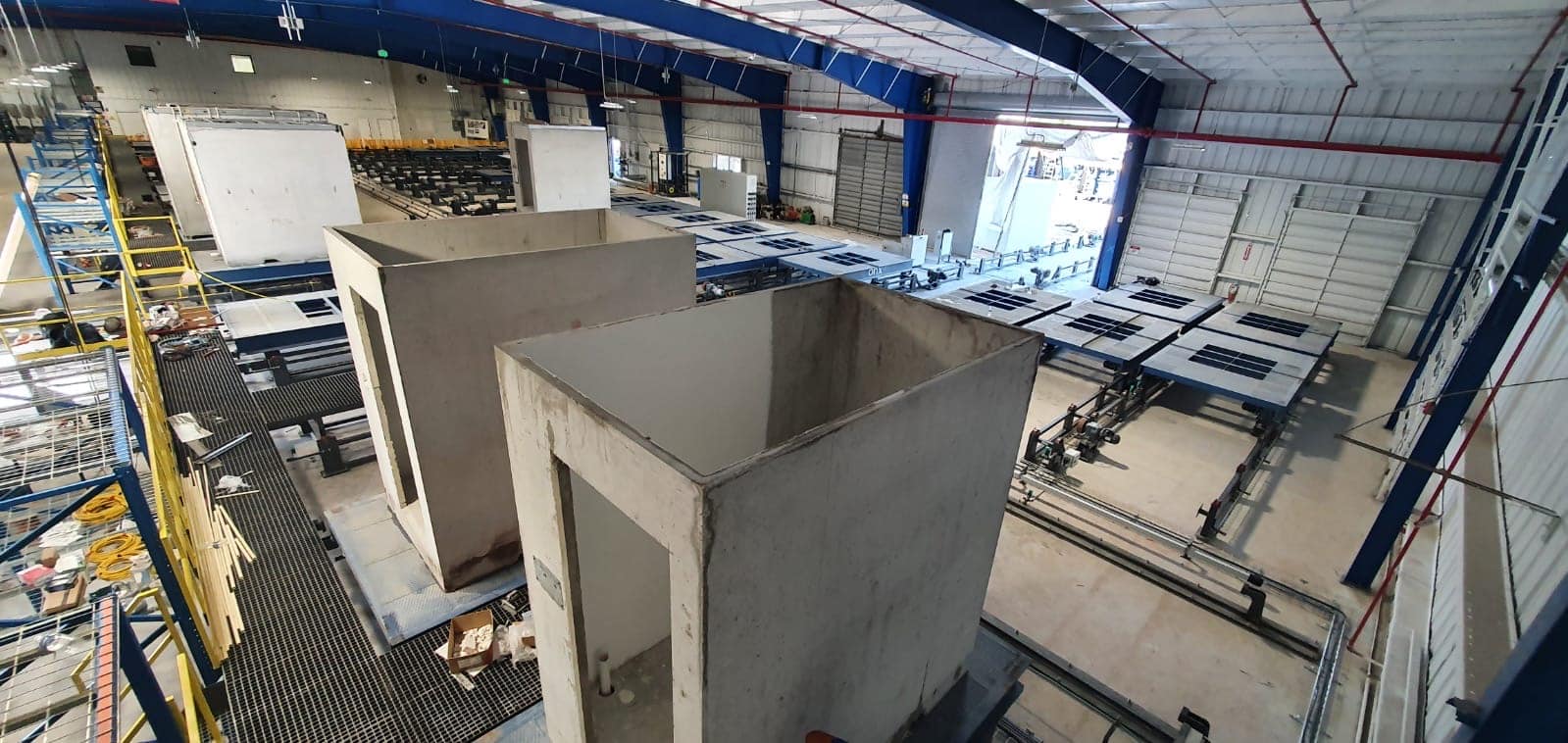
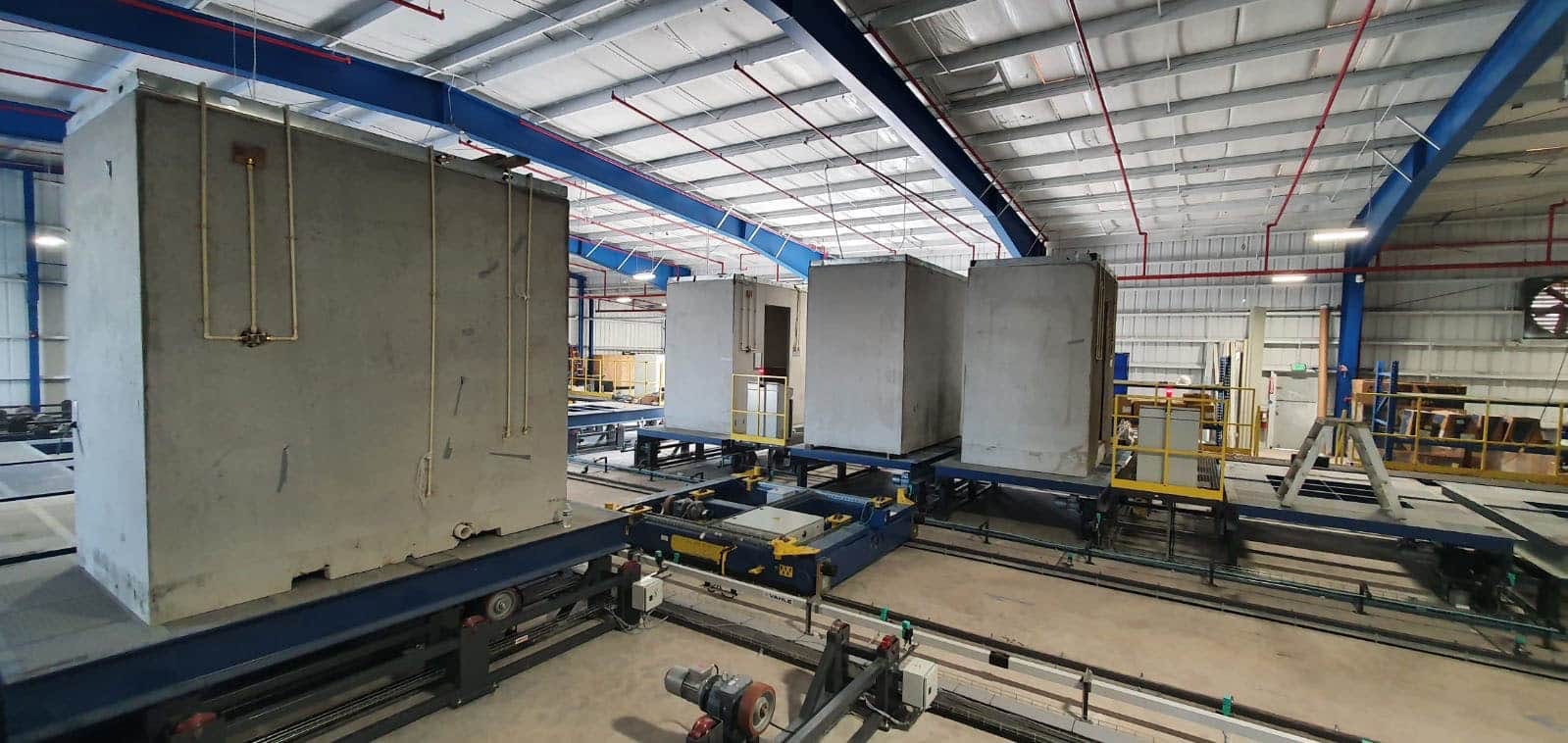
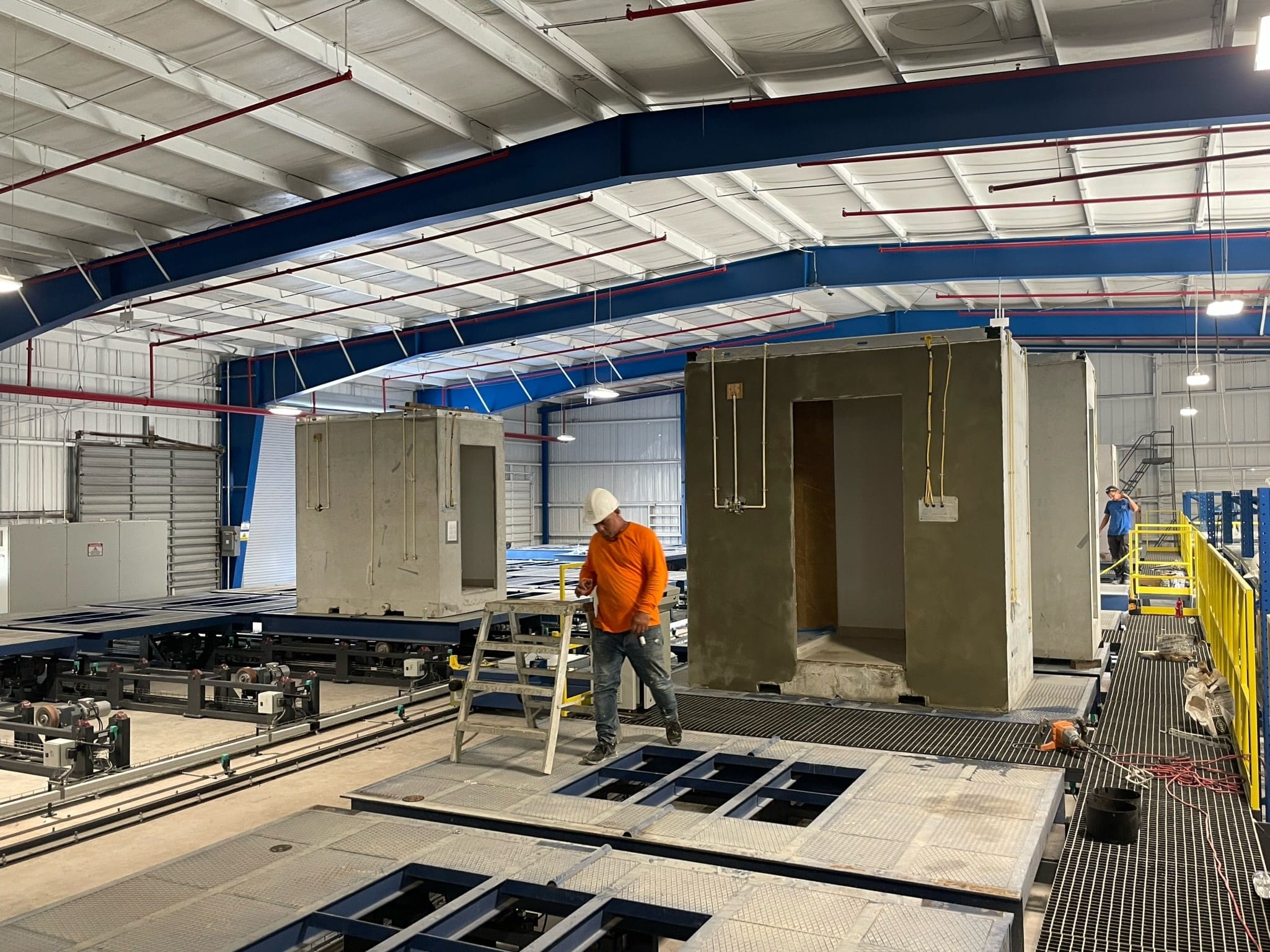
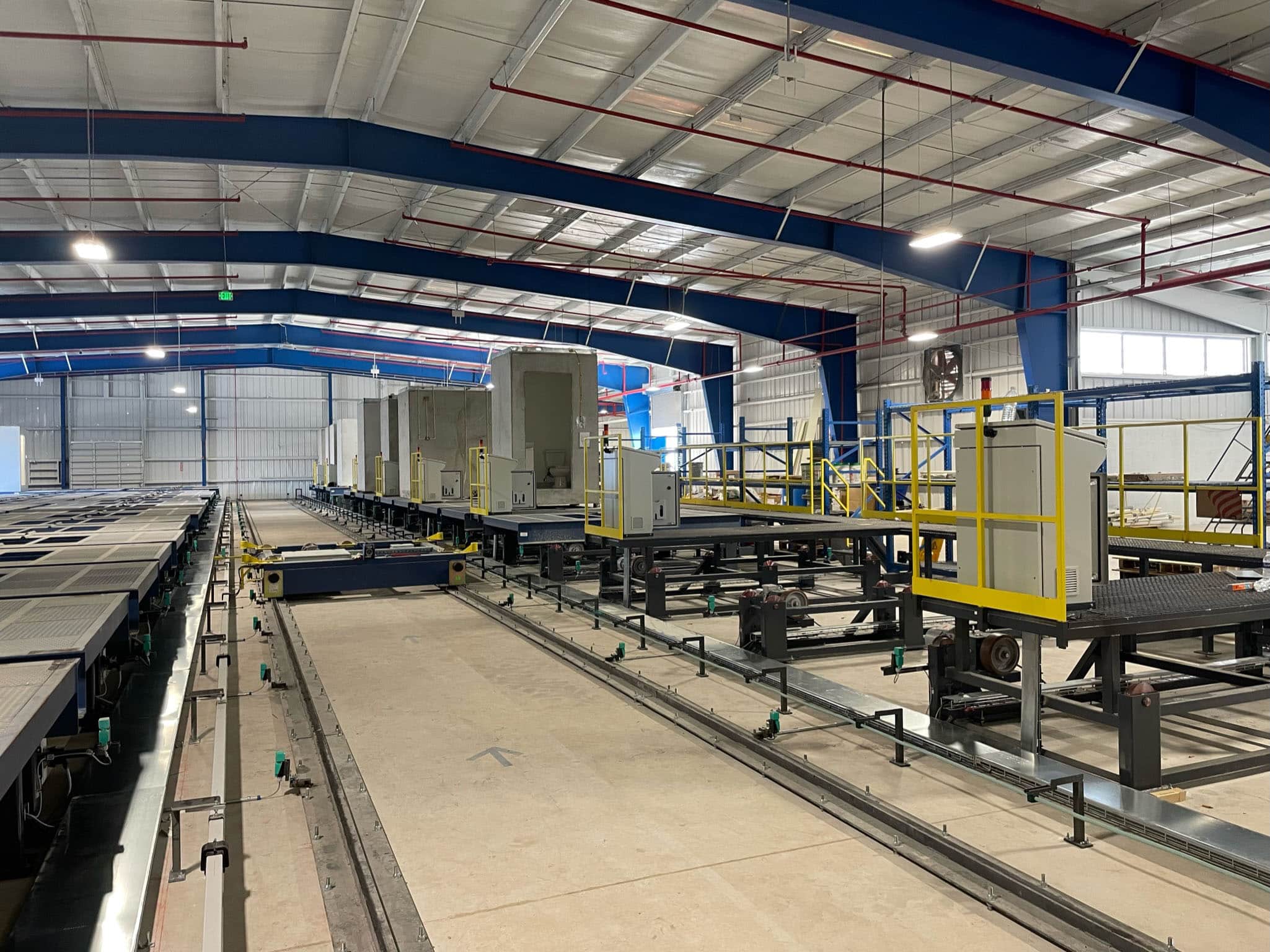
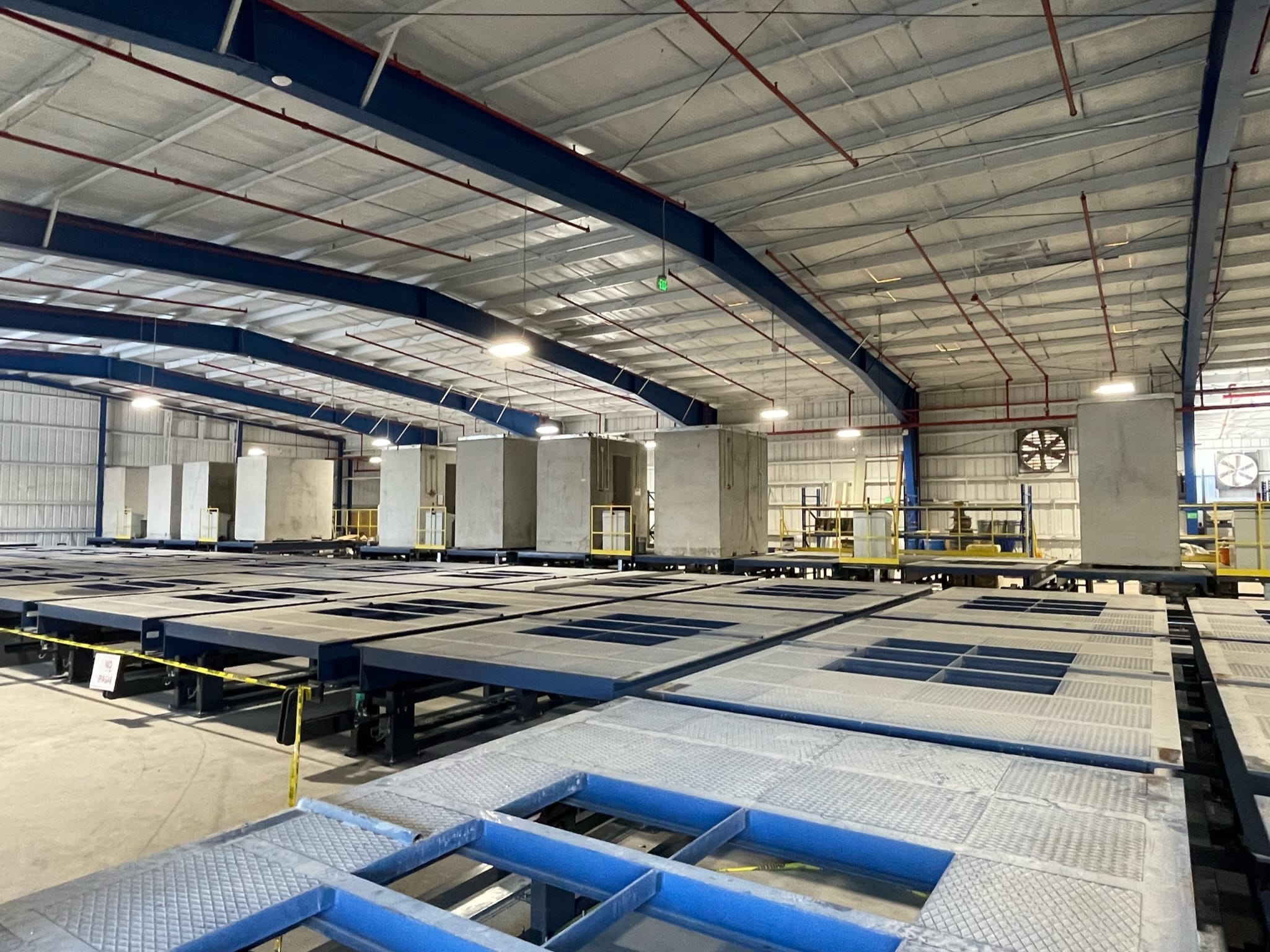